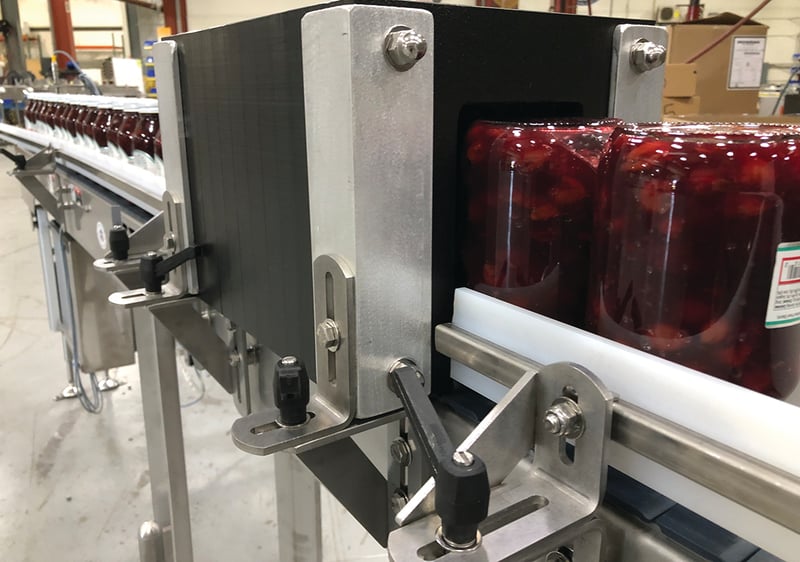
Hot-Fill Glass Jar inversion conveyor with missing cap reject
Multi-Conveyor recently built a system to replace a manual hot-fill-jar-inversion process while providing optimum cooling time after the capper for multiple products and jar sizes canning line at a renowned family-owned produce manufacturer in northern Wisconsin.
Single-lane-filled glass jars exit an existing capper in an upright orientation, then side transfer at the Multi-Conveyor infeed conveyor. The product conveys to a non-powered jar inverter and travels approximately 30-seconds upside-down, prior to entering a second non-powered jar inverter. The jars then side transfer to an existing conveyor in an upright position.
The conveyor length was critical for cooling of the up-to-200°F product, both before and after the 90° side-flexing curve, and prior to the final inversion. Jars then proceed to an existing labeler and staging system where the product is manually removed and ultimately case packed.
This line produces jams, salsas, pie fillings, and other products. Multi-Conveyor added dual belt drive assemblies prior to the first inverter, ensuring accurate inversion of larger, heavier jars.
A missing and cocked-cap reject prior to the first invert that included sensors, logic, and reject completed the system.
Regarding increased production and ease of changeovers, the customer explained, “On average we can produce 20-40% more per day. The new equipment with additional line space also gives the flexibility to allow the filling line to continue running a bit longer than before. Last year we handled about 350 cases (4200 jars) per day and now are averaging about 500 cases (6000 jars)”.