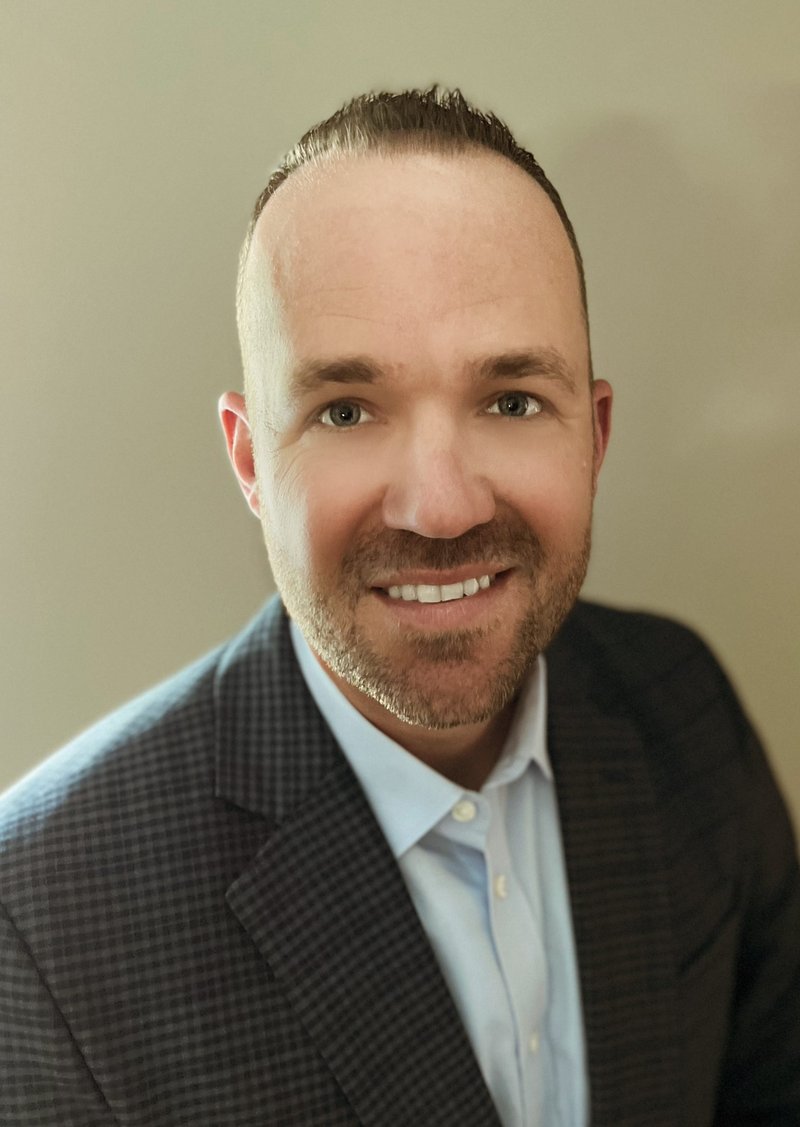
Value-added services can add an additional revenue stream to your dealership
2501 Rosegate
Saint Paul, MN 55113
Phone: 913 829-1000
Back in February’s edition of Wholesaler, I wrote about ‘forklift battery management’ to your dealership’s services offering as a one-stop shop solutions provider. Subsequently, the topic of optimizing forklift battery management as a value-added service to your end-customer while being an additional revenue stream for your dealership.
I recently got the opportunity to catch up with Dustin Love, Business Development Manager, at Flight Systems Industrial Products, and he was able to provide some inspiration and content for this month’s article. So, with that, let’s dive into battery chargers, charging lead-acid vs charging lithium-ion batteries, and the intricacies of charging.
As technology advances, the demand for batteries continues to grow, and with it comes the need for efficient charging solutions. Lead-acid and lithium-ion batteries have distinct charging requirements. Understanding these differences and offering specialized services, your dealership can increase service revenue while providing optimal charging solutions for your customers.
Prolong Battery Life
A battery’s performance is only as good as its charger. When paired correctly, a quality battery charger will prolong battery life and provide maximum run time. When selecting the right charger for your end-customer’s application, there are many variables to consider, such as:
- Vehicle type (for example, industrial vs golf car)
- Power Source
- Battery Type (Lead-Acid – Flooded, AGM, Gel or Lithium-Ion)
- Battery Size (Voltage & Amperage)
- Connectors and Accessories
- Charging time and specifications
Charging Lead-Acid
Unlike lithium-ion, there is no special communication technologies or internal battery monitoring systems (BMS) monitoring the cells and communicating with the charger. To charge a lead-acid battery you can simply supply current at the correct rate using the main battery’s positive and negative connections. Regular maintenance, such as equalization charging and periodic water level checks, testing, and monitoring healthy charging tendencies is crucial to ensure optimal performance and extend battery life.
It is important to use a charger designed for lead-acid batteries. Lead-acid batteries can be charged using older technology from the 1950s–60s, which is very dependable, but they can also benefit from using a newer high-frequency switching charger. High frequency chargers typically require more maintenance, but they offer higher efficiency, healthier charging, and up-to-date technology with programmable charge curves.
Charging Lithium-Ion
Lithium-ion batteries also benefit from a charge rate based off its amp-hour capacity. Proper charging tendencies are not as crucial with lithium, so it can be charged faster and still be considered a healthy rate. It’s important to avoid overcharging or discharging the batteries excessively. Additionally, temperature monitoring during charging is crucial to prevent overheating. These batteries should be charged using chargers that are specifically designed for lithium-ion technology and set to the recommended voltage and current levels.
Lithium-ion battery technology sometimes is marketed as being maintenance free, but those with experience know that is not the case, it’s just a different kind of maintenance needed. Instead of cycling and equalizing charging to ‘boil out’ lead-acid sulfation, the ‘maintenance’ aspect of it is more programming adjustments to the lithium charger and BMS technology on the battery, such as updates and troubleshooting.
Setting Up the Battery Charger
Follow the battery manufacturer’s guidelines and use chargers specifically designed for the battery chemistry when setting up a charge for both lithium-ion and lead-acid batteries. Following the recommended charging practices ensures optimal performance, maximizes battery life, and ensures safety during the charging process.
A lead-acid charger will need to be set with the correct voltage, output current, and standard connector type. More advanced lead-acid operations will use a battery identification device (BID) on the charger that can program itself automatically for various kinds of lead-acid batteries and monitor its performance.
A lithium charger’s set-up is determined by the battery manufacturer’s design. In the material handling industry, there is no standardization for chargers such as DC connectors, auxiliary connection pinouts, BMS protocol signals, etc. Setting up a charger for lithium entails working directly with the battery manufacturer to develop a working charger that communicates with their battery specifically.
Safety
In both battery types, you must incorporate safety considerations when setting up a battery charger. Charging lithium-ion batteries requires extra caution. Lithium-ion batteries are sensitive to temperature extremes and can be damaged or even become a safety hazard if charged improperly.
Lithium batteries are equipped with an integrated battery management system (BMS) to optimize their performance and ensure safety. Acting as the control center for individual batteries, the BMS prevents overcharging and over-discharging, safeguards against potential hazards, monitors battery health, balances charge across cells, and promptly shuts down the battery if unsafe conditions are detected, protecting both the battery and the user.
Lead-acid batteries are generally less sensitive to charging conditions, but proper ventilation and monitoring for hydrogen gas are still essential for safety. Also, be sure to check the battery manufacturer’s specifications for recommended charging voltage thresholds.
As Dustin Love mentions, “Maintain to sustain! Properly maintaining your batteries is important for their longevity. A battery that is routinely serviced will significantly outlast a neglected battery. Knowing how to maintain your battery is the first step.”
So, consider adding ‘forklift battery management’ to your dealership’s service offering to enhance the longevity of your customer’s electric forklift fleet’s batteries, reduce downtime, and ultimately boost their productivity.
About the Author:
Chris Aiello is the Business Development Manager at TVH Parts Co. He has been in the equipment business for 16-plus years as a service manager, quality assurance manager, and business development manager. Chris now manages a national outside sales team selling replacement parts and accessories in various equipment markets such as material handling, equipment rental, and construction/earthmoving dealerships.