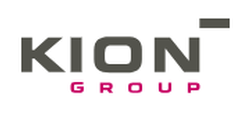
KION Group closes recycling loop for lithium-ion batteries
2450 West 5th North St.
Summerville, SC 29483
Phone: 843 875-8366
Fax: 843 875-8329
http://www.kiongroup.com
-
Intralogistics Group’s batteries now being recycled by strategic partner Li-Cycle in Magdeburg, Germany
-
Sustainable process recovers up to 95 percent of the battery’s valuable minerals and materials
-
KION Group CTO Henry Puhl: “We are helping to drive forward the transition to a low-carbon economy.”
The KION Group is now sending lithium-ion batteries that have reached the end of their useful life to its strategic partner Li-Cycle Holding Corp. (“Li-Cycle”; NYSE LICY) for recycling. The Group’s objective is to have a total of up to 5,000 tonnes of end-of-life battery material professionally and sustainably processed at the Li-Cycle recycling plant in Magdeburg, Germany, by 2030. This tonnage is equivalent to around 15,000 large lithium-ion batteries of the kind used in forklift trucks.
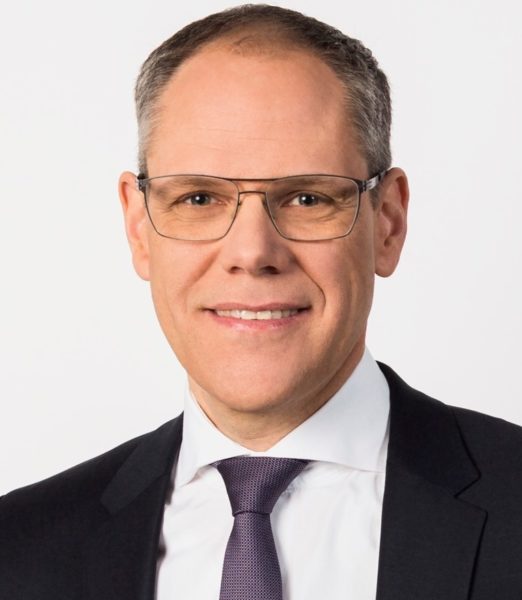
Henry Puhl
“We firmly believe that lithium-ion is the drive technology of the future. That is why it is so important to us to make the technology part of a closed loop – from manufacturing and usage through to resource recovery,” said Henry Puhl, Chief Technology Officer of KION GROUP AG at the official opening of Li-Cycle’s first recycling plant in Europe.
The KION Group produces its own lithium-ion batteries at the KION Battery Systems plant in Karlstein am Main. These are then installed in the electric-powered industrial trucks of the KION brand companies Linde MH, Fenwick, STILL, and Baoli, as well as in automated warehouse logistics systems. “Together with Li-Cycle, we are now closing the loop and ensuring that nearly all of the valuable materials, including lithium, cobalt, copper, and nickel, are recovered from the lithium-ion batteries used in our trucks. These resources can then be used to make new batteries.”
Puhl emphasized that the partnership with Li-Cycle will strengthen the KION Group’s sustainability credentials and further extend its market-leading position in electric-powered industrial trucks. While 88 percent of all industrial trucks sold by the KION Group brands last year were electric, the figure for the global market as a whole was just over 70 percent. “Not only are we helping to drive forward the energy transition, but we are also leading the way in the recovery of critical materials and the recycling of advanced lithium-ion batteries.”
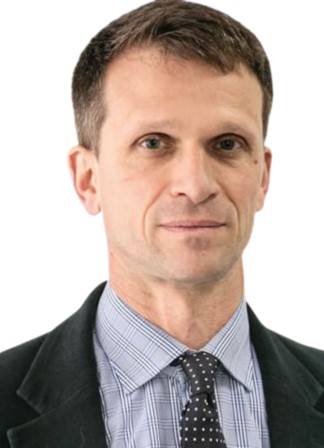
Richard Storrie
“We want to ensure that lithium-ion batteries do not end up in landfills, but instead that all their components are recycled in an environmentally responsible manner,” explains Richard Storrie, Li-Cycle’s President for the EMEA region. “The agreement with KION is an excellent example of a sustainable, long-term cooperation. Acting as a strategic partner, Li-Cycle will support the KION Group in hitting its recycling targets while at the same time helping it to meet EU requirements for battery management.”
Modern and environmentally friendly recycling process
Li-Cycle uses an innovative and sustainable two-stage process to recycle lithium-ion batteries and recover critical battery materials.
In contrast to energy-intensive smelting methods, Li-Cycle uses non-thermal liquid-based size reduction technology. Li-Cycles technology can be used to process all types of lithium-ion batteries – regardless of shape, size, or chemistry. This liquid-based process is safer and avoids potential hazards such as fires. After the plastics and metals (copper, aluminum, and steel) are separated, they are rinsed, dried, and packaged ready to be shipped. The remaining intermediate, known as black mass, is then dealt with in stage two. In this hydrometallurgical process, materials such as lithium carbonate, cobalt sulfate and nickel sulfate are recovered from the black mass so that they can then be used in new batteries.
The Li-Cycle process at its recycling facility in Magdeburg produces only minimal landfill waste, low air emissions, and no wastewater discharge. It has processing capacity for up to 30,000 tonnes of lithium-ion battery materials per year.