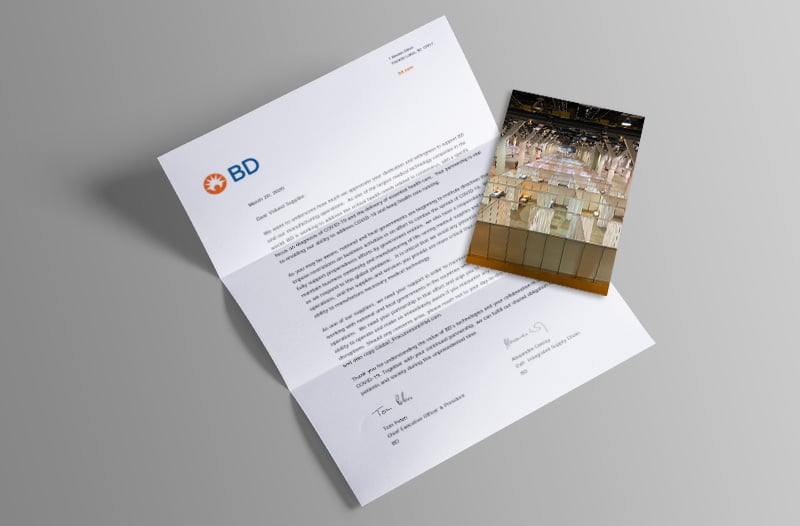
Flexcon supplies medical containers to field hospital
For Ken Beckerman, it all came down to one picture of McCormick Place, Chicago’s expansive convention space, wall to wall with hundreds of makeshift hospital rooms constructed to meet the expected wave of coronavirus patients. With it was a thank you letter email from a customer he’d never met for a container delivery he’d almost forgotten.
The experience provided a nice lift during these days of social distancing and came as a complete surprise. You see, weeks earlier, the McCormick Place containers were just another order with odd specs, a pinched timeline, and an unidentifiable buyer. The fact that the containers would play a part in something this significant never occurred to him. And even if it had, it might not have changed anything.
Over the past weeks of the pandemic, Flexcon has responded to corona virus-related requests and regular ongoing requests with commitment. Team members were focused on getting the job done, and in many ways, the current environment is giving the company a chance to do what they do best. “We get excited about a challenge, and we love to come through for people,” says Ken Beckerman, president, and CMO of Flexcon. “A lot of times we don’t even know if our orders are corona virus-related. A lot of it is indirect. We’re just focused on keeping customers going efficiently and safely and keeping supply chains moving.”
How Flexcon is contributing
Some of the projects that are known to be supporting COVID-19 prevention and response efforts include providing hundreds of bins in varying sizes to the field hospital that was set up in Chicago’s McCormick Place. The color-coded containers were created on a rush basis and delivered to Becton, Dickinson, and Company—the end-client on the project.
Flexcon also provided containers for vials and laboratory equipment used in support of Medtronic’s work making critical, lifesaving products to treat COVID-19 conditions.
Abbott Labs, a company on the leading edge of creating rapid tests for the coronavirus, ordered specialized containers related to their operations during the pandemic. On an accelerated timeline, Flexcon designed and prototyped models to meet the customer’s specific requirements.
Flexcon is also doing a project for an automation company that works with Amazon in Europe. As an example of the times, it is not known what the containers will be used for, but it is COVID-19 related and the need is urgent.
Providing stress-relief is a key service attribute in these days of the pandemic, and Flexcon is stepping up. “Medical companies have a lot of things to think about. We’re relieving them of one major part of their jobs that they’d have to manage, monitor, and stress about. We’re taking that off their plate so they can focus on other things,” Beckerman explains.
Continuity during crisis
Maintaining continuity during a crisis is a hard-won trait for Flexcon. Their experience during Superstorm Sandy made the company conscious of the need to be prepared to serve customers continuously in the event of any natural disaster or economic disruption. During that event, Flexcon went without services for two weeks.
In the time since, the company has installed Virtual Private Networks (VPN) for all of its employees, which has enabled them to work from home without interruption. Additionally, they have dispersed container production among a dozen facilities. As a result, the company has remained fully operational during the current crisis.
Keeping things moving
That continuity has benefitted Flexcon’s non-medical customers as well during the pandemic. The need for help finding the right container or right solution for transportation has not slowed down. Customers building distribution centers have schedules that rely on the totes, bins, and plastic pallets Flexcon provides. So far during the current crisis, Flexcon has been able to continue supporting them. “No one wants to be held up,” Beckerman says. “We’re a small piece of a big puzzle and if we don’t do our part, the puzzle can’t be completed.”
Business, as usual, has been business as unusual of late. Flexcon has had to institute all of the protective protocols to continue work in onsite locations. In order to meet spacing requirements, the company has adapted by adding shifts rather than crowding team members together.
No matter what the coming weeks of the COVID-19 crisis look like, Flexcon is committed to providing customers with the containers, and continuity, they need. “We just continue to do what we do to help make today’s medical and economic challenges a non-issue for our customers so they can get what they need when they need it,” Beckerman says.