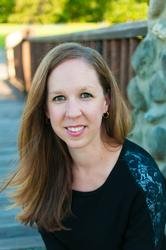
Robotics and technology bring expanded efficiencies to warehouses
As the material handling industry works to quickly and accurately meet customer needs while navigating labor and supply chain trends, in certain situations automation can fill some of the gaps. This month, Material Handling Wholesaler looks at a few of the latest developments in robotics and driverless forklifts, along with exploring overall warehouse automation strategy.
Transforming forklifts
Balyo specializes in transforming standard forklifts into driverless robots, offering tools that simplify the shift from manual to autonomous material handling, according to a company press release. The robot Balyo Reachy, for example, can pick pallets of up to 1.5 tons to a height of 37 feet and achieve a 360-degree turn in only 9.9 feet, the release said. Many companies are scaling up instead of out, according to Mark Stevenson, Balyo’s chief sales officer. “The only way to safely and efficiently be part of this vertical revolution in materials handling is to automate the storage and retrieval of goods,” he said, in the statement.
Rob Patey, marketing and digital director, said a two-shift operation sees a return on investment in utilizing Balyo technology in about two and a half years. “And if you’re a 24-7 operation, you’re going to get a return on investment right out of the gate,” he said. The company’s automated guided vehicles include all of the functions needed, according to Patey. “All of the brains are on board the robot,” he said, noting there are sensors and cameras and lasers on the AGV to identify what to pick and drop.
Balyo is a global company, according to Patey. “We started in France and Germany and two years ago shifted to start focusing on the U.S.,” he said, noting the focus in the States on alignment with consumer demands. “People want to get things to their house the minute they order them. There is a lot happening on the back end to make that happen,” said Patey, noting how the trend is driving the need for third-party logistics providers. He said Balyo is always improving the technology of the robots themselves, including better cameras, better lasers, and guidance tech. “There are less errors and a smoother sense of operation,” said Patey, adding that the technology can “better identify and navigate and increase safety. “On the software side, we’re building tools, working on the tools to make the process go smoother,” he said.
Other companies also offer options for warehouses.
Vanderlande, which bills itself as a global partner for future-proof logistic process automation in warehousing, airports, and parcel sectors, showcased a modular workstation leveraging an item-picking robot at the recent ProMat, according to a release. Some of the solutions showcased included: the Fastpick suite of goods-to-person picking solutions, which includes Goods-to-Picker 2.0 and Adapto, according to a press release.
The former is a second generation of Vanderlande’s modular workstation and is designed to simplify the picking process, the statement said. “Leveraging the benefits of 1:1 picking and exceptional ergonomics, it improves pick performance while reducing errors and training,” the release said. Adapto is a roaming shuttle-based automated storage and retrieval system, with advanced sorting and sequencing capabilities that work with a variety of cartons, trays, and totes, according to the company.
Dual-mode options
Others point to the advantage of equipment designed with dual-mode capabilities. At Crown Equipment, Jim Gaskell said automated forklifts provide the flexibility of operating in manual modes, further enhancing the flexibility associated with mobile automation.
Gaskell, director of global automation and emerging technologies for Crown, said the dual-mode operation should be considered an essential feature of an automated forklift. Dual-mode forklifts have been designed “from the ground up as automated vehicles while retaining the flexibility to operate in manual mode when required,” Gaskell said. “With automated dual-mode forklifts, warehouses can operate more predictably, have greater visibility into product movements, and don’t have to compromise the versatility that makes forklifts so valuable to warehouse operations,” he said. “Because the lift trucks are integrated with the warehouse management system, there is continuous visibility into their location as well as the loads on the forks, and the vehicles can perform consistently over multiple shifts.”
Other technological advances gaining speed include telematics and data analytics, according to Gaskell. “Telematic systems can play a vital role in implementing forklift automation, identifying potential use cases, informing your automation strategy, measuring performance, and helping you ensure access,” he said.
When to automate
Gaskell recommends strategically planning an automation investment. “Any effort to introduce automation into your facility should be guided by a realistic plan with achievable expectations that can also be scalable based on success and growth,” he said, adding that realizing tangible benefits requires “the right frame of mind.”
That means looking beyond industry hype and unrealistic expectations, Gaskell said.
What should be considered are the genuine operational challenges and the tangible goals sought to be accomplished, according to Gaskell. “You must also identify the tasks and equipment within your operations that are good candidates for automation,” he said. The more processes are standardized, the better the interaction of automated forklifts within the environment, Gaskell added.
“It is important to understand that not all warehouse tasks are candidates for automation. It depends on the available technology, the amount of customization and complexity involved, and how easy it is to incorporate new workflows and processes to integrate the automation,” he said. Warehouse managers need to identity tasks and equipment that are well-suited for automation, according to Gaskell.
“Some warehouse tasks that have shown to be ideal candidates for automation include load transportation throughout the warehouse, pallet put away and retrieval and order picking,” he said, advising considering how forklifts are being used and how and when pallets are moving when looking at automation. “Many of today’s challenges, including hiring issues, supply chain disruptions, and changing consumer demands can be resolved or significantly diminished with automation technology that exists today,” Gaskell said.
At Balyo, Patey agreed. Meeting labor needs is one of the biggest drivers of interest in automated technology, according to Patey. “That’s the number one conversation we have. People walk up to our booth and say, ‘I can’t get drivers,” he said.
Bridging the gap
Patey stressed that the learning curve for Baylo technology is manageable. “Everybody thinks of robotics and thinks it all is complicated,” he said, noting the marketing department for Baylo is working this year to help customers understand the technology is “not a big scary change.” “They really don’t need to fear it,” he said.
The other concern frequently raised about robotics is that the advancements will take over jobs and operations, according to Patey. “We’re still so far away from that. The algorithms are just not there. Artificial intelligence does not have its own self-direction,” he said. Balyo’s robots can be operated fully manually and autonomously, the release said.
This helps bridge “the perceived gap between whether to use people or technology,” said Stevenson, in the statement. “This frees up people to focus on improving operations and other truly value-added activities. In this way, our technology is being used to vastly improve people’s working lives,” he said. Sometimes just getting started with automation is the hardest step, said Gaskell, stressing the importance of an informed, strategic approach.
“This clears the path to identify the right automation technologies and warehouse tasks to be automated,” he said. “It is important to understand that you are not simply automating a manual task. You should look at the entire process or workflow impacted by the introduction of automation.”
About the Author:
Eileen Mozinski Schmidt is a freelance writer and journalist based in the Greater Milwaukee area. She has written for print and online publications for the past 14 years. Email [email protected]. If your company would like to be featured, email [email protected]