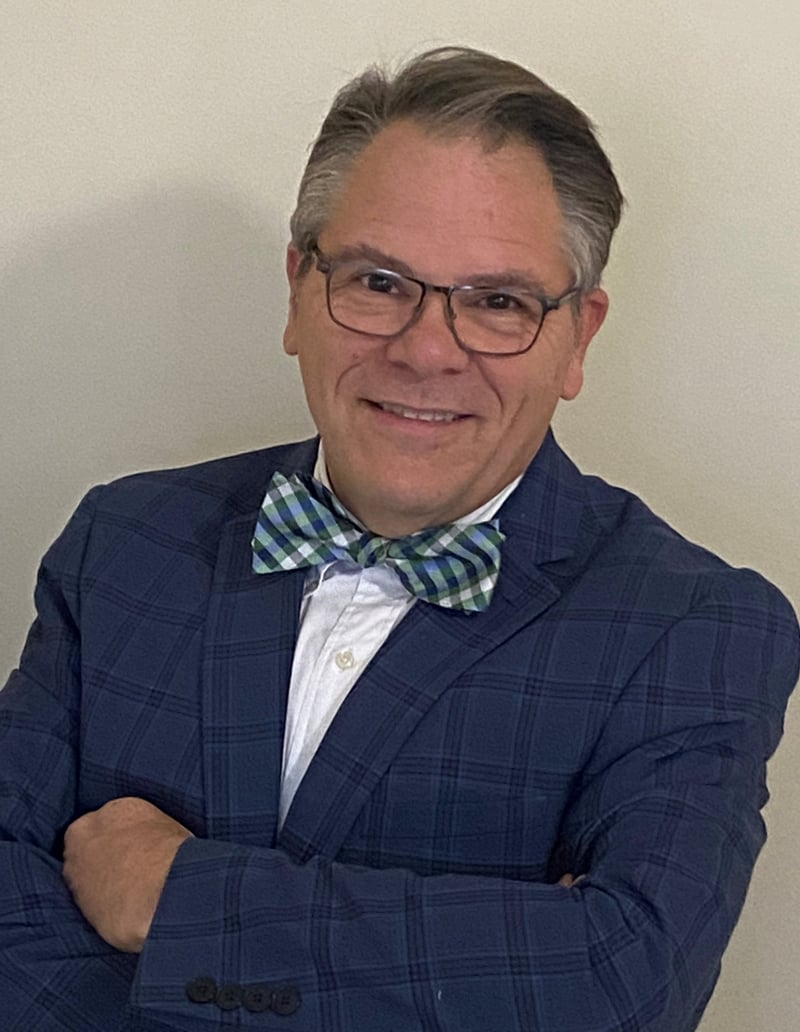
Material Handling Professionals continue to choose Propane over alternatives
Why propane forklifts are cleaner and more productive
Many challenges are facing material handling operations today—labor, rising energy costs, supply, and demand issues. It makes choosing the right equipment crucial. Propane-powered forklifts have been around for more than 70 years, and yet some professionals still have doubts about the capabilities, efficiency, and environmental impact of this equipment. Here are a few reasons why material handling professionals should choose propane equipment over electric or diesel.
Propane forklifts are more cost-efficient
Many companies that are looking to reduce emissions have noticed that it can sometimes come with a higher price tag. With propane forklifts, companies can reduce emissions more cost-effectively than other energy sources.
Propane forklifts offer cost savings throughout ownership. The capital costs of propane-powered forklifts can be up to 30 percent lower than those for electric when factoring in the equipment needed for battery recharging according to the Propane Education & Research Council (PERC). Propane helps avoid these extra expenses, saving money for other line items like new employees, additional training, or business development, to name a few. Businesses operating on propane may also be able to lock in a mutually beneficial fuel contract with their local propane supplier for more savings and financial peace of mind.
Propane forklifts increase productivity
PERC’s survey showed that 68 percent of forklift fleets are required to work both indoors and outdoors. In contrast to many electric models, propane forklifts can be used in both indoor and outdoor applications, including when the temperature is at or below 0°F (-20°C). Plus, propane is much cleaner than diesel, which produces toxic exhaust that makes it unsafe to operate diesel-fueled equipment indoors. Propane’s versatile, the low-emission operation makes it possible for forklift operators to safely work wherever the job is, keeping them more productive throughout the day.
No matter the job or location, propane forklifts provide powerful, reliable performance. Electric forklifts can’t carry the weight of large jobs, and diesel forklifts aren’t the best fit for smaller tasks. A propane cylinder’s life expectancy is three times longer than that of an electric forklift battery, and it often extends beyond the typical lifespan of the forklift itself. A propane cylinder can also be refilled at any time without impacting its lifespan.
Typically, one propane cylinder provides consistent, 100-percent power throughout an eight-hour shift, so facilities and warehouses can function at uninterrupted operational capacity. In comparison, batteries may only power an electric forklift for as little as four hours and may require hours of recharging along with strict battery management. Propane forklifts work anywhere, anytime so employees don’t have to worry about downtime for recharging.
Propane forklifts are more sustainable
Propane is a clean, low-carbon alternative energy source and, when used to power forklifts, can reduce sulfur oxide (SOx) emissions by 76 percent compared with electric equipment and nitrogen oxide (NOx) and hydrocarbon emissions by 94 percent compared with diesel models, according to PERC.
PERC published a research paper, Fork(lifts) in the (Off) Road: Should We Ban Internal Combustion Engines for Electric? that compares the lifecycle emissions profiles of propane and electric-powered forklifts. Findings show that in most states, propane forklifts are the cleaner option compared with electric forklifts, especially when considering marginal electric grid emissions. The case for internal combustion engine (ICE) forklifts becomes even stronger with hybrids and renewable fuels. In fact, nearly all propane ICE forklift technologies emit extremely low criteria pollutants compared to the regulatory standards.
The analysis used available engine certification emissions data published by the Environmental Protection Agency (EPA). The study found that 314,000 ICE forklifts are operating in California alone. Replacing all ICE forklifts in the state with battery-electric forklifts would require nearly 10 GWh/day of additional charging capacity. This is important as forklift managers across the US work to navigate new emissions requirements for Class 4 and Class 5 forklifts. The California Air Resources Board (CARB) is pursuing a ban on all equipment that uses diesel, propane, natural gas, and gasoline—and mandating the use of battery-electric and hydrogen fuel cell electric forklifts only.
When selecting a forklift energy source, companies making the choice between electric and propane-powered equipment often rely on the fact that electric equipment produces zero emissions during operation but tends to overlook its full emissions profile, which includes well-to-wheel emissions. Propane produces significantly fewer lifecycle emissions than both diesel and electric and is the best choice for businesses interested in reducing their carbon footprint.
Propane continues to be the preferred energy choice for material handling professionals. Propane forklifts’ ability to work around the clock, reduce emissions, and keep costs in check are just a few reasons that business owners count on them to get the job done.
To learn more about using propane for material handling, visit Propane.com/MaterialHandling.
About the Author:
Joe Calhoun is director of off-road business development for the Propane Education & Research Council. He can be reached at [email protected].