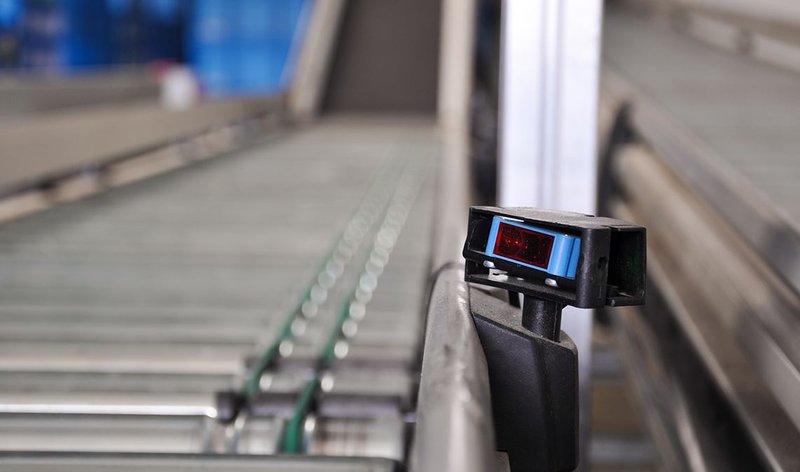
Improving maintenance in manufacturing
The digital universe is doubling in size every two years, growing from 4.4 trillion gigabytes in 2013 to 44 trillion in 2020. Enterprises have responsibility for around 85 percent of the data held in this digital universe, according to the EMC Digital Universe with research and Analysis by IDC report.
Manufacturing plants are just one type of enterprise contributing to this data production, by choosing to collect process data in order to monitor machinery status. Here, Claudia Jarret, US country manager at automation parts supplier EU Automation, explains how plant engineers can make the most of this data and ensure their maintenance schedule benefits their plant.
Manufacturers, faced with the constant pressure to keep up with customer demand while remaining flexible, are acutely aware of the threat of plant downtime. Caused by a multitude of factors, including machine failure, downtime can cost manufacturers up to $260,000 per hour, according to research by analyst firm Aberdeen Research.
Therefore, preventative maintenance, where equipment is maintained before it breaks, is essential, rather than reactive maintenance, which focuses on fixing equipment following a breakdown.
But for those in high volume, low margin industries such as food and beverage or automotive parts manufacturing, preventative maintenance may be wrongly seen as unattainable, due to perceived high upfront costs.
Prevention
The days of waiting for a system to fail due to overheating motors or leaking heat transfer systems, for example, are thankfully behind us. Plant managers now plan regular inspections, upgrades, and troubleshooting to avoid breakdowns. These simple steps are one way in which preventative maintenance can be carried out.
But as Industry 4.0 technologies such as condition monitoring become more accessible, there are even smarter, more accurate, and less time-consuming methods available.
Many manufacturing plants now use predictive maintenance, a sophisticated form of preventative maintenance, to establish how well equipment is functioning and accurately predict failures before they occur. Not only does this reduce the risk of downtime-causing breakdowns, but it can also mean any necessary replacement parts can be ordered and are in stock in case of equipment failures.
In addition, monitoring the health of equipment can allow for gradual tweaks, where a huge overhaul would previously have been required for improvements. Alterations can improve the efficiency of processes, ultimately reducing costs by eliminating inefficient elements and increasing equipment lifespan through maintenance or replacement of wearing parts.
Where to start
The first step a plant manager should take when implementing any preventative maintenance schedule is to gather as much data as possible. Crucially, this should include an accurate estimate of the real cost of downtime to the particular plant in question. Collating data collected by smart sensors, sales figures, and retrofitted systems should allow you to take into account loss of sales, wasted products,s and the cost of emergency repairs, which can provide a useful baseline figure.
Using their experience of the plant, maintenance engineers should also be involved to produce an ideal plan for the plant, including areas they believe will require higher levels of maintenance, such as older equipment or machinery that is inherently prone to breakdowns such as motors, turbines, or other moving parts.
This plan can then be used alongside the budget to produce a realistic maintenance plan, including what level of preventative maintenance can be employed. For some manufacturers, this will mean regular equipment checks, such as once a month for a section of the plant, or daily for more volatile machinery.
Data
If true predictive maintenance is chosen, data such as temperature, pressure, and vibration are collected by sensors and will be continually integrated, stored, and analyzed. The next question for manufacturers is how to make the most of these valuable, but large, data sets.
Once the data has been collected, the next step to make the most of its potential is to begin analysis. One popular option for data analysis is a cloud analytics service. Here, raw data is transmitted to the cloud, where it can both be stored and analyzed for trends that can predict an event including a breakdown. Many services also incorporate an alert system and warnings of impending breakdowns can be sent via a web portal, app, e-mail, or text message to relevant personnel.
Other manufacturers, perhaps concerned about cybersecurity, the long-term stability of data stored in the cloud, or the lag between data collection and analysis, will choose to undertake the analysis of raw data in-house. Although this is often significantly more resource-heavy, it does give plant managers complete control over their data.
Obsolescence
Regardless of which system is implemented, predictive maintenance can be used to manage obsolescence, in addition to reducing downtime and improving process efficiency.
This means parts can be ordered at the correct time to suit the maintenance schedule. Traditionally, manufacturers would have to keep a stock of parts that may need replacing, which take up valuable space on the plant floor that can instead be used for operations. Spare parts can also be bulky and produce a health and safety hazard, including trip or fire hazards if stored on the plant floor.
Instead, manufacturers can choose to order replacement parts only when necessary, maximizing the space and resources they have available to them. With suppliers such as EU Automation able to ship obsolescent parts worldwide within 24 hours, there is now no need to store parts on-site or to suffer extended periods of downtime waiting for them to arrive.
Preventative maintenance is essential for manufacturers to reduce downtime and the vast amounts of data now being produced by plants can be effectively used for predictive maintenance. When predictive maintenance is employed, the data collected can also be used for other purposes, such as increasing process efficiency and ensuring replacement parts are ordered in plenty of time. Therefore, proper collection and analysis of this data are essential to maximizing its potential and this will only become more important each year as the quantity of data increases.