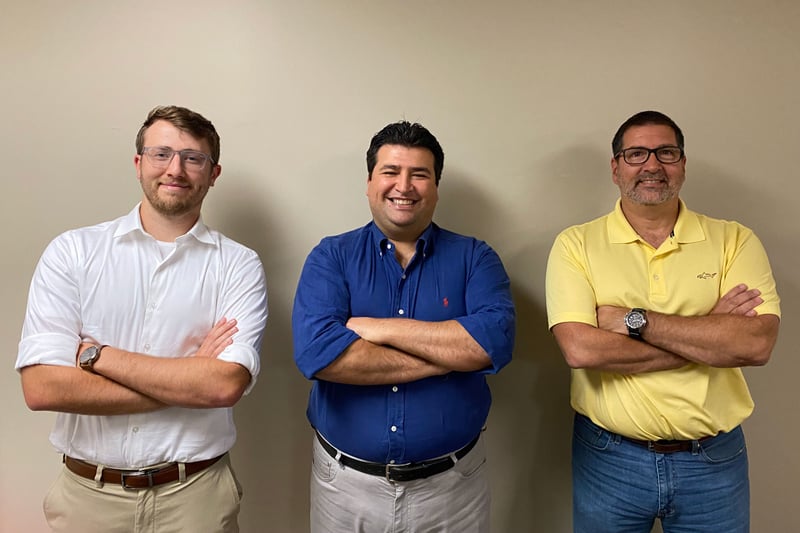
Excel Composites expands sales team
Following huge private and public infrastructural funding across North and Central America, global composites manufacturer Exel Composites has invested in expanding the sales team based at its factory in Erlanger, Northern Kentucky. The team serves customers in the North and Central American markets as well as opening up customers to Exel’s global network. Now the team is looking to increase the awareness and benefits of pull-winding technology.
This introduction comes at a time when governments across the Americas are looking to invest multi-billion, even trillion, dollar infrastructure packages to rebuild and futureproof power grids, transportation systems, and telecommunications networks. For example, Biden’s $1 trillion Bipartisan Infrastructure bill will provide $89.9 billion to expand public transport, helping to replace obsolete vehicles with clean, zero-emission vehicles.
With huge growth expected in these segments, the team is well positioned to help new customers take advantage of composites to solve challenges, drawing on its experience in business development and the technical expertise honed from many years of working with plastics, injection molding, and pultruded composite companies.
Drawing on experience
Over several decades of navigating the European markets, Exel has successfully positioned itself as an expert in manufacturing lightweight, robust, and long-lasting carbon fiber and fiberglass composites for transportation, power grid infrastructure, telecommunications, buildings, and construction. The company’s pultrusion and pull-winging processes are highly automated compared to manual manufacturing techniques, which ensures continuous, high-volume production of composite profiles at a consistent quality.
“The American market was one of the first to accept the benefits of pultrusion. Thanks to the acquisition of the well-established North American pultruder Diversified Structural Composites (DSC) in 2018, the potential of the benefits of pull-winding to fill a gap in the market also became apparent”, explained Francesco Ierullo, Head of Sales for the Americas markets at Exel Composites.
He continued, “Like pultrusion, pull-winding pulls saturated fibers through a heated die. The main difference is that the fibers can be organized in a crosswise or longitudinal alignment, depending on the application’s requirements. This cross-directional control of mechanical properties makes pull-winding the ideal manufacturing process for composite hollow profiles with thin walls. For building materials, this is important because it means the material’s weight is kept low, fewer resources are wasted during manufacturing, and production costs remain manageable”.
Being a world leader in pull-winding technology, Exel Composites is well placed to bring these solutions to the American markets where there are almost no companies using this production process. The company aims to do this with the help of Ierullo, Head of Sales, and two Area Sales Managers.
About the team
Ierullo has worked with Exel Composites in Europe since 2015, recently relocating to Erlanger from Italy to help strengthen the company’s visibility. He is joined by two Area Sales Managers for North America, John Mertic and Marc Tagher, and a North American Sales Representative, Roger Gastineau.
Mertic brings his experience managing the sales for multimillion-dollar accounts to help increase Exel’s market share across the continents in a targeted, strategic manner. His expertise in telecommunications, electrical composites, and conductor cores will allow Exel to grow in line with the pending infrastructural investments across the Americas. Tagher’s technical skills gathered from 25 years in the field of engineering make him an ideal consultant and collaborator for a growing customer base. He specializes in airports, defense, aerospace and marine transportation, and construction. Gastineau, the American agent for transportation, has been an integral team member at Exel for many years.
Exel combines a large but local ‘made in USA’ manufacturing footprint with the expertise of a global company to provide efficient sales support, technical consultancy, and customer service from its Erlanger factory. The company has seven production factories throughout the globe, providing manufacturing support and the development of specific products in targeted applications. The team’s collaborative, forward-thinking approach to manufacturing will ensure an efficient service while helping customers overcome their challenges with composite solutions.