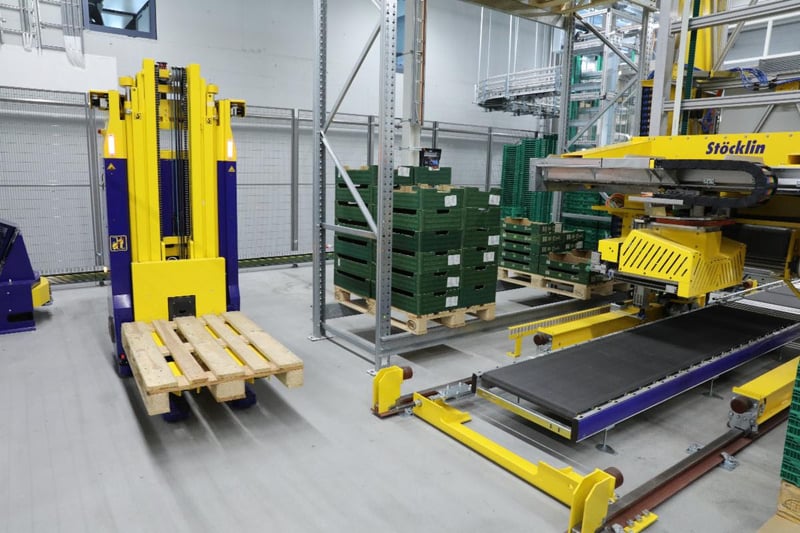
Stoecklin introduces CasePicker Automation Solution to help produce companies improve throughput performance
New system accommodates different size containers to optimize palletizing and depalletizing while ensuring product integrity
Increased demand for fruit and vegetables across retail and foodservice channels is driving suppliers to enhance their supply chains with automation and other tools that make the transfer of product more efficient and effective, while reducing waste. Stöcklin Logistics, a supplier of innovative supply chain solutions, is launching Stöcklin CasePicker to address the specific product logistics challenges and opportunities now facing produce shippers.
The Stöcklin CasePicker offers a completely automated solution for distribution centers serving hundreds of retail outlets, with freshness zones from 4°C to 14°C and up to 135,000 cases/day for fruit and vegetables. It features a depalletizer with intelligent control that manages a unique special gripper with a suction strip and underride plate to ensures gentle and reliable case picking. In addition, the gripper allows different returnable and disposable containers to be picked immediately after another for the first time.
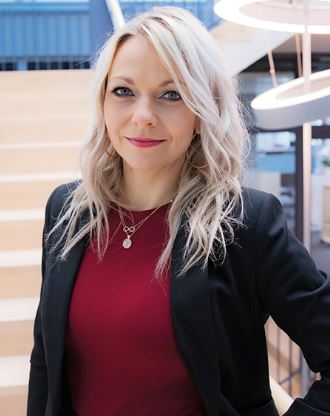
Damaris Grütter
“Until recently, varying types of containers were a major impediment to automated depalletization and subsequent direct palletization on pallets for each specific retail outlet. Conventional automated picking systems depalletized the entire pallet and separated the contents on trays in one initial step, which took a lot of extra time and increased the opportunity for product damage and waste. The Stöcklin CasePicker addresses all of these pain points plus dramatically improves throughput performance,” said Damaris Grütter, Director of U.S. & Canada for Stöcklin.
Keeping with Stöcklin policy, this Stöcklin CasePicker is completely modular and scalable. Depending on the required performance, it can be upgraded by adding new modules and used in combination with proven Stöcklin equipment such as the FTS Eagle-Ant picking and conveying equipment. In addition, the modules are simple to integrate into existing buildings and structures as well as capable of docking with existing systems.
The Stöcklin CasePicker ensures that only the intended goods are picked directly from the produce pallet for the retail-outlet pallet which prevents unnecessary movement. In addition, the system speed depends on the order volume. This process optimization and variable utilization reduces the energy required in comparison to conventional solutions.
“The Stöcklin CasePicker is completely scalable and ensures simple modular integration into existing distribution centers. The number of workplaces can be reduced by two-thirds. The remaining personnel experience a considerable improvement in the quality of their workplace as well as a significantly healthier working environment. This system, therefore, provides a truly employee-friendly alternative to the prior system of strenuous manual picking,” said Lothar Käufler, Head of Development at Stöcklin Logistics,