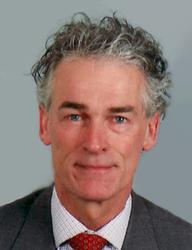
BEUMER focuses on Total Value of Ownership in product development:
Companies should take into account more than just overall operating costs if they want to be competitive in the long term. An integrated approach is far more important. By looking at the Total Value of Ownership (TVO), the effectiveness of business investments can be described more comprehensively, from the right perspective, and therefore more meaningfully. It is important to include economic as well as ecological and social aspects when developing machines and systems, as the BEUMER Group does, making it not just a supplier but a strategic partner for postal and CEP companies.
“The pressures on postal and CEP companies in a competitive environment are increasing. Not only must they save costs but they must also reduce environmental impact and respond to influential market trends,” describes Martin Mossinkoff, globally responsible director of the business segment “Logistics Systems”. These include new technologies, the increasing use of new sales channels such as e-commerce – which raises high customer expectations for immediate deliveries – and also growing globalization. As a result, the demand for more efficient sortation and distribution systems continues to grow throughout the world.
For example, the gross domestic product in many countries in Asia is steadily increasing which, in turn, is leading to an increase in wages. This is particularly noticeable in China and India. A new middle class has come into being which is significantly changing the consumption pattern of the population in the developing countries. The volume of trade is increasing and purchasers are demanding ever-shorter delivery times. “This is also affecting the working environment, for example in distribution canters. Here too, it is becoming necessary to think and act more globally whereas local orientation of such service providers is reserved for niche markets,” says Martin Mossinkoff. Postal and CEP companies must therefore be able to adapt flexibly and dynamically to changing requirements in order to survive in the marketplace.
Investment for improved competitiveness
“The trend towards automation continues to be important for the survival of service providers, and is therefore strongly increasing in distribution centres. Material flow technology is becoming more complex, and systems must be able to carry out more flexible tasks or be adapted to suit changing local situations,” Mossinkoff explains. Highly efficient processes are required to enable parcels to be dispatched to customers quickly.
For example, e-commerce and mail order companies have recently also been offering products which, up to now, have been difficult to transport automatically because of their dimensions. However, the automation of existing solutions or the integration of new machines and systems is usually accompanied by significant costs for the user. To enable them to make these strategic investment decisions in a targeted manner, companies must analyze all direct and indirect costs in advance in order to calculate the Return on Investment. In doing so, they should set their sights on more than just the procurement and operating costs.
To enable companies to work efficiently, their machines and systems and the associated production processes must be directed towards long-term customer benefits. “That’s why we develop all solutions with an integrated approach, the Total Value of Ownership (TVO),” says Mossinkoff. “While the Total Cost of Ownership (TCO) exclusively takes into account the economic aspect of a product, TVO is based on and includes ecological aspects such as energy-saving operation or resource-conserving production as well as social factors.” Examples of these include sorters which run very quietly and therefore produce only a small amount of vibration. This makes for a more pleasant working atmosphere and less noise pollution.
The systems also simplify the sorting of goods of all kinds, and this is carried out automatically instead of by hand. This enables our customers to describe the effectiveness of their business investments holistically and more meaningfully. Companies are not only able to determine their direct costs, but, above all, the ‘Total Value’ of the solution to be supplied over its entire operating life. For this purpose, we identify three interacting factors: market developments, risk management and longer term sustainability.
Adapting flexibly to increasing demands
“To enable companies to flexibly convert or adapt their machines and systems, for example to accommodate changes in consumer behavior or to adapt to trends such as the increasing use of e-commerce, we collaborate with the users to work out which solution is able to accomplish the required task and whether it will also be capable of meeting future requirements,” Mossinkoff describes. The decisive factor here is whether performance can be increased without also increasing the costs in the long term such as in the case of inefficient sorter drives or if maintenance is frequently required.
An important point is therefore the availability and usage of machines and systems that have been supplied and installed. Malfunctions and machine shutdowns frequently lead to long downtimes, especially in intralogistics. Production and delivery can come to a complete halt. Possible risks must be clearly identified, analyzed and evaluated. “As a strategic partner, we therefore take care of our customers from the initial project meeting to the running system and beyond. As part of this service, we offer flexible agreements, an efficient supply of spare parts and comprehensive training for users of our systems,” states Mossinkoff. As an example, these agreements can include upgrading of the systems by our customer support staff as soon as new sorting technologies and software controllers are introduced. It is important to BEUMER not only to rectify faults, but also to help companies to satisfy future performance and technology demands. For example, as the mechanical parts of a sorter wear out over the years, staff must respond immediately at the first signs to prevent possible consequential damage. The BEUMER Group is therefore in a position to offer high system availability over the whole working life. “Our objective is always to make processes even smoother in order to ensure a value-added material flow,” Mossinkoff adds.
The third factor relates to sustainability. This subject, in particular, represents a particular challenge for intralogistics. In order to find a clear answer to the question of sustainability of a system, machine or drive, BEUMER has developed a validation system in the form of the BEUMER Sustainability Index (BSI). We use this to systematically and continuously measure sustainability on every new machine and also on existing solutions. Each of the three levels, economy, ecology and social, is divided into five categories for evaluation purposes using the BSI. These include “efficiency and effectiveness”, “lifetime”, “operating costs”, “production-related raw material consumption” and “training and development standards”. These categories are evaluated with up to five points. The total of these is used to provide a classification into the levels “excellent”, “very good” and “suitable for improvement”. If a product is classified as suitable for improvement, BEUMER subjects it to reengineering to ensure that it achieves a higher level.
Designed for growth
BEUMER’s product base includes modular high-performance sorting systems, which enable widely varying goods – such as parcels, products in bags and bulky goods – to be sorted, distributed and checked in large quantities quickly, reliably and accurately. For example, a customer who wanted to fulfill his global commitment to sustainability and environmental protection in his distribution centre through efficient sorting technology also approached us with a requirement for fast and accurate sorting. “We installed our energy-saving Cross Belt and Tilt Tray Sorters. After all, most of the energy in this center was used in operating the sorting and conveyor equipment,” Mossinkoff reports. “Because our solutions use linear synchronous drive technology, the energy consumption is 75 percent lower than that of sorters with conventional technology.”
The process here is sophisticated. Workers place the boxes with the products from the warehouse on a conveyor belt. This takes them to an in-line sorter, which transports the parcels to one of three possible positions, depending on whether the goods are to be dispatched in batches or mixed in newly assembled boxes. At one station, boxes are sent directly to the dispatch sorter. Another station receives boxes that contain items in certain batches, which are then sent to the infeed unit of the pre-sorter. The third station is designed for boxes containing items that are brought together for mixed deliveries. These are delivered directly to the warehouse, where workers remove the items from the boxes and place them on shelves. They can then be taken as required and placed in plastic trays on the conveyor system. The conveyor transports the trays to a further conveyor on Level 2 of the building. The trays and the boxes with the batches are brought together and emptied. Workers place the items on the Cross Belt Sorter. This automatically sorts the goods from the plastic trays into defined containers, which are discharged in the tilt area. From here, they are transported by a system of conveyor belts to the workers, who place the items manually on the final sorter, a Cross Belt Sorter. The chutes are equipped with batch divider flaps. These are activated when a complete batch has been delivered. The batch is thereby isolated and can subsequently be packed in a box by the operator. The box is pushed onto a roller conveyor, which transports it to the Tilt Tray Dispatch Sorter. We have integrated the system and device controllers for the machines seamlessly into the user’s warehouse management system. This prevents bottlenecks, and the customer achieves faster throughput.
Long-term service ensures reliable operation
BEUMER has entered into a three-year service contract with the customer to offer maximum operational reliability. As part of this agreement, service engineers are stationed on site, with responsibility for the support and preventative maintenance of all material flow equipment and for management of the local spare parts stock. This agreement also includes upgrading the systems when new sorting technologies and software controllers are introduced which illustrates how total value of ownership can be more important than just the cost of the equipment.
Thanks to the sorting systems and software controllers used, the distribution centre works more efficiently than conventional installations. The company has also achieved a number of important objectives, including greater operational efficiency, flexibility and freedom from errors on dispatch. The handling costs and the energy costs have decreased, and the environmental impact of the operations has also been reduced.