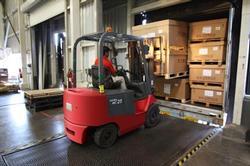
Top reasons Forklift Accidents & Injuries occur in a Warehouse
There are several common reasons accidents and injuries occur in a warehouse or distribution center. If your facility monitors these situations and makes continual improvements, accidents and the associated costs can be avoided.
Beyond the physical and emotional impact of an accident, the average work-related injury leads to $38,000 in direct expenses and $150,000 in indirect costs. This means that a single injury could cost your business a total of $188,000.
For the employer these costs include:
- The loss of productivity;
- Reimbursement costs and expenses to the injured employee;
- Salary of the injured worker and their downtime replacement;
- Equipment, repair, or replacement costs;
- Changes to insurance premiums;
- Legal costs; and
- Lost business opportunities.
Most accidents involve docks, forklifts, conveyors, materials storage, and manual lifting and handling. Here’s a look at the most common accidents and how to avoid them.
- Slip and fall.
This typically occurs because of improper lifting, pushing, pulling, and reaching while on a wet surface or an area without guard railing. Increase preventative measures and use safety railings to address slip, trip, and fall hazards.
- Overturned forklifts.
Approximately 42% of forklift fatalities result from the operator being crushed by a tipping vehicle. Many of these result from carrying a load that is too heavy for the equipment.
Loads should always be checked carefully for stability before moving them. Operators should also know the limits of the pallet racking systems and ensure each load is tilted back with the forks sitting low during transport.
- Pedestrian injury.
These injuries often result from inadequate signage, slippery floors, and poor enforcement of pedestrian safety protocols around forklift traffic areas. They can also be caused by forklift operators exceeding the speed limit. Place warning signs in high traffic or poor visibility locations and use telematic vehicle monitoring to sound an alarm when speed limits are ignored.
- Forklift operator complacency.
It’s easy for drivers to become complacent when doing repetitive work. Operators need reminders, retraining, and reinforcement of best practices on an ongoing basis. Monitor and identify driver attention deficits.
Telematic monitoring can prevent accidents
It is easier to prevent accidents when you know what causes them, which requires historical and real-time data. An advanced telematics system can deliver:
- Insight on driver behavior — good and bad — so poor habits can be addressed, and good practices can be reinforced.
- Customized safety checklists that stop vehicle operation if the operator skips steps, the forklift has a mechanical issue, or the driver fails to complete safety protocol.
- Advance location capabilities that facilitate optimum traffic management and optical location that allows speed limits to be set for each type of forklift. If speed is exceeded, an alarm sounds and an email is sent to the supervisor.
- Data on warnings and trends, allowing management to implement their risk-mitigation plan.
The warehousing industry’s fatal-injury rate is higher than the national average for all other industries combined. But action prevents accidents, and telematic monitoring can help identify where proactive measures are needed.
Topics: dangers of forklift operation, routing, forklift impacts, safety versus productivity, operator behavior, limit risks, accident reporting