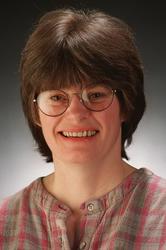
Safety roots protect work, home and life
A culture of safety at work prevents accidents, saves down time and money, and might even keep employees safer at home.
Companies identify risks well, said Mark Micheles, vice president of sales in North America for Safety Today.
“But getting employees to change their behavior and make safety a habit is what will have the biggest impact on a company’s incident rate and safety performance. An integral, behavior-based safety culture is a must,” he said. “For example, in the glass-handling market, employees are taught how to handle glass and panes. They are also taught the proper PPE to wear and when and how to wear it. But behavioral training goes deeper. It imagines a worst-case scenario, because, frankly, accidents don’t happen with any regularity, so we behave differently when they do. So, in this market, employees must be trained how to behave if a sheet of glass starts to fall. Their first instinct is to try to catch it or stop it, which can be a fatal move when working with sheets of glass. Instead, you have to change that ingrained behavior and teach employees to move away from the hazard — the falling glass — rather than trying to intervene.
“Here’s another example of a behavioral threat in a warehouse: A large automotive manufacturer has forklifts traversing the whole floor. There is a process in place that requires employees walking through the warehouse to stop at each intersection before they cross an aisle, look both ways, and then physically point in the direction they are going to continue walking. That’s a behavioral adaptation to a potentially hazardous environment. So, if employees are observed just walking through a warehouse while talking to another person or with eyes glued to their cell phones, they can be reminded of the hazard and retrained in the safe behavior protocol.
“In both of these situations, the foundation for safety is there. The risk has been identified, and the company has put a safety protocol into place. It’s the behavior of individuals that’s really the threat, and teaching or reinforcing safe behavior is the solution. Here is where the rubber hits the road: Unless employees change their behavior, a safety culture won’t take root,” Micheles said,
If it does take root, it can grow into safety away from work – the drive home and the drive in, avoiding sleep deprivation and being distracted by cell phones.
“I think most companies try to go well beyond the baseline today versus years past,” Micheles said. “The baseline is just that; it only scratches the surface. I’ve engaged with several customers who have created or asked us to create home safety programs. These are companies who are very proud of their safety records, and people want to work for them because of it. We constantly ask ourselves, how do we break through that baseline to go well beyond the regulatory issues? How can we help our employees and our customers’ employees? We truly take safety as our mission, not just our business. To that end, we’ve dedicated parts of custom catalogs to at-home safety.”
But the culture of safety begins at work.
“Safety is always first. In the event of an emergency, I believe that each team member must be trained to evacuate the facility safely and must rehearse the procedure and demonstrate proficiency,” said Rhonda Kovera, chief executive officer of Visual Workplace Inc. “The need for evacuation is often rare, but when it becomes necessary, efficiency and accuracy is crucial. Evacuations will be more effective when the necessary information is displayed and practiced.
“Many companies are using glow in the dark materials to provide illuminated exit paths. Others have visually displayed pre-designated meeting points, outside the facility where team members gather to take a head count. Both strategies increase the successfulness of any evacuation.
“Recordable injuries drive the innovation and introduction of new safety products. Companies invest a tremendous amount of resources in training, products and continuous learning to keep their employees safe. A successful business culture focuses on safety as its number priority followed by customer satisfaction,” Kovera said.
“Visuals are the core of an efficient, productive workplace. They are meant to identify normal and abnormal situations, reduce injury, direct behavior, eliminate missing information and reveal opportunities for improvement. Visual management is the foundation of all continuous improvement. Without visuals, questions soar, information is lost in translation and mistakes are made,” Kovera said.
Signs need to be large enough to be seen, placed properly and have a simple, direct message, she said.
“Signage that is too small for the space will vanish and never be seen. To quickly determine an effective size for your sign, there is a simple rule of thumb: your sign should be one inch in height for every foot off the ground the sign will be hung. For example, if your sign will be hung 24 feet from the ground, the sign height should be at least 24 inches to achieve the best visibility. The width of the signs should be proportionate to the content,” she said.
As the economy improves and business picks up, “manufacturers try to fit more products into the same space while maximizing inventory turns,” said Tom Smith, product marketing specialist at Brady. “This means more human resources and foot/forklift traffic picking, packing and shipping more products which increases the potential for accidents. This places a greater emphasis on efficient traffic flow and clear communication methods to stay safe.”
“Product innovation is driven by the need to help employers stay compliant and keep workers safe,” Smith said. “Brady looks for markets or conditions where safety or identification solutions don’t exist and seeks to fill them. Whether it’s labels that adhere to frozen cryogenic vials, safety lockout devices that didn’t exist before, or an efficient process to mark electrical wires, Brady looks for unmet opportunities to challenge our research and development teams.”
Nationally, about 100 employees are killed and 95,000 injured in forklift accidents in all industries. “Add to this the fact that the fatal injury rate for the warehousing industry is higher than the national average for all industries, and it is clear why the need for innovative safety products is needed,” Smith said.
Safety signage is key, he said. “With these visuals in place, workers can quickly identifying appropriate aisles, racks and locations for picking and storage and minimize time spent searching for the proper storage or bin locations. Stop, yield, speed limit and other traffic signs alert pedestrians and material handlers to traffic flow, guidance, limitations and intersections. Floor signs will alert pedestrians to forklift traffic. Fire, eye wash and SDS signs provide quick identification of nearby fire extinguishers, first aid stations and chemical information at a glance.
Only trained, authorized people should run equipment. With one innovation, just as you have to have a key card to enter a building, you have to have a key card to start a forklift.
Anything with an on/off switch, from a coffeemaker to a crane, can use AccessPoint from Whiting Passport, said Joel Phelps, product manager.
Other systems track where machines are and what they are doing. “This adds ‘the who’,” Phelps said. “User authentication is made at the point of use.” It records when equipment was used and for how long.
It’s part of a culture of safety to keep workers safe, reduce risks of equipment misuse and prevent damage to machines and products.
AccessPoint does not need a network to function, he said. That saves money and time, because if a network-based system is down, no one can use any equipment. One client is Disney, which uses the access cards to make sure no one unauthorized starts driving a golf cart at the resorts and without having to spend on a network.
“How a piece of equipment is operated has a lot to do with how long it lasts,” Phelps said.
It can also simplify pre-shift safety inspection records. Instead of a paper copy that is turned into a supervisor and filed, a user-created checklist can be used on a smart phone or tablet. “Every operator signs off. It is archived and easily searchable. It is a huge risk mitigation factor,” Phelps said. “As technology becomes more ubiquitous, I firmly believe it’s going to be seen as negligent not to have access control.”
The technology did not exist until it was created for the Australian mining industry, which had very expensive machinery below ground.
“Proper operator training is at the foundation of a safer and more productive operation,” said Jay Costello, director of training at Hyster Company. “The ‘right’ mix of training is subjective and depends on the application, operator and equipment. In any case, it should be site-specific, truck-specific and application-specific, and each facet of training—formal instructions, practical training and performance evaluation—plays a major role in the overall success of the program.
Forklifts should be designed with safety in mind, but that does not lessen the responsibility of the operators. These safety features are only as effective as the driver implementing them. Operators should not become too dependent on forklift equipment features, such as stability systems that can give them a false sense of security. Although these features can enhance the overall safety of the truck, they are not a replacement for diligent and attentive driving.”
Pedestrian signs should warn about where lift trucks will be, and if possible, companies should set separate travel zones for trucks and people. Mark out of order trucks with ‘do not operate tags’ and move them away from other trucks, he said. “It is absolutely essential that (a) operators are properly trained; (b) only trained, certified and authorized operators are permitted to use lift trucks; and (c) those trained and certified operators use the lift trucks in an appropriate manner,” Costello said. “Prevention is critical. At Hyster, we engineer our lift trucks to enable a trained operator to safely utilize the trucks. While Hyster® trucks are safe, durable and reliable, there is no replacement for diligent and attentive operation.”
Properly trained lift truck operators can help reduce lift truck downtime and accidents, limit lost-time injuries and workers’ compensation costs, improve driver efficiency and minimize product damage—evidence that a thorough and effective training program enhances productivity, health and the bottom line, he said.
“As technology has advanced over time, lift truck manufacturers have built more safety features into their trucks, and materials handling operations have focused more on accident prevention and instilling a culture of safety in the work environment,” Costello said.
Mary Glindinning is a freelance writer who has worked at daily and weekly newspapers for more than 20 years. She lives in rural Shullsburg, Wis. E-mail [email protected] to contact Mary.