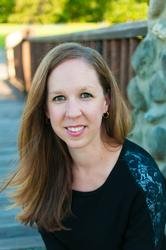
Safety at Work: How training and technology help achieve goals
No matter the size or type of material handling organization, safety is frequently a top consideration.
How to keep employees safe, operate equipment smoothly, and keep a facility in good working condition all play into such decisions.
OSHA cites that the most frequently reported cause of lost or restricted work time is work-related musculoskeletal disorders caused by routine lifting of heavy objects, daily exposure to vibration, routine overhead work or work with the neck in a chronic flexion position, according to Don Buckman, divisional environmental, health and safety manager for Hyster Company.
“Proper ergonomics can help reduce stress and injuries associated with the overuse of muscles, bad posture, and repeated tasks. It also plays a part in maximizing the productivity of lift truck operators,” he said.
Buckman said ergonomic experts at Hyster focus on providing features offering lift truck operators easier entry and exit, improved foot space, better body position, and enhanced visibility.
Training and product design
Hyster’s customers rely on robust, OSHA-compliant training programs, customized to their specific trucks to help operators become proficient users, according to Buckman.
“Intensive applications must maintain constant vigilance when it comes to safety, and work to overcome challenges like widespread skilled labor shortage and high turnover,” he said, noting that immersive reality simulators are helping Hyster customers supplement operator training without taking equipment out of service.
At ProMat DX in April, Hyster highlighted two award-winning designs that can help workers maintain an ergonomically sound operating position, according to a company release.
The examples included the new cab design for Hyster Big Trucks and the J50-60XNL, which “prioritize operator comfort and performance with features built to provide easier entry and exit, improved foot space and enhanced visibility,” the statement said.
Lift truck telemetry systems can also help in creating a safety culture and in improving operator accountability, according to Buckman.
“Onboard sensors that track truck information by the specific operator provides visibility to their travel locations, idle time, and impact alerts,” he said, noting that the system can identify performers who may require more training.
“The system can also limit truck performance based on operator skill level. For example, new hires might have their trucks capped at slower speeds to help reduce potential risk while more experienced operators can still operate the same truck at levels that allow maximum performance,” Buckman said.
At Hyster, Buckman recommended that companies stress that operators and supervisors stay focused on safety.
“In addition to ergonomics and other safety features like lights and alarms, technology can help businesses reinforce operating best practices,” he said.
A product-driven safety boost
At Custom Industrial Products, safety is an associated benefit of its product lines. The company, founded in 1995 by husband-and-wife team Henry and Darlene Taylor, is Florida-based.
The company manufactures VRC Material Lifts for integrators, architects, and material handling companies.
The products offer a host of safety benefits, said Rob Railis, director of business development.
“The VRC’s themselves help with the area of safety,” he said, noting their work in moving materials out of the way in a warehouse and in preventing forklift injuries.
“This is a fairly low-cost way of improving the safety, especially when compared to elevators,” Railis said.
The cost of a VRC is about a third to a quarter cheaper than the cost of an elevator when considering maintenance, inspections, and related personnel, said Jake Jakobson, manufacturing engineer for Custom Industrial Products.
The VRC features benefits for operators as well.
“In a lot of ways it is an ergonomic feature, moving materials from one floor to another,” said Jakobson, comparing the difference to the risks to using a ladder, moving products by stairs or transferring from floor to floor lifting the product overhead with a forklift
“Ergonomically, it helps to prevent injuries,” he said.
Jakobson said the units are designed for industrial use and with safety in mind, in some ways mimicking such features found on elevators although in a quicker fashion.
The (VRCs) are programmed to stop quickly when needed and feature braking systems designed to stop with overrated loads. The systems are also certified in the state of Pennsylvania, which is home to a program of certification.
“It allows us to sell within the state of Pennsylvania, but also tells the customer we are going the extra mile,” Jakobson said.
All units meet 508A standards for control systems and incorporate additional safety measures, according to Jakobson.
“We have a push-button station which will tell you whether the door is open or not or whether the doors are latched. There is a secondary indication if a program has occurred in the system. It will not allow you to operate until the major fault is cleared,” he said.
The products also include a safety locking system that will not allow the system to operate if anything went wrong with the loading of products.
Custom Industrial Products has customers ranging from small to large, and therefore including somewhat different safety considerations, according to Jakobson.
Smaller operations are more concerned with basic safety, he said.
“They like that we put in a tell-tale diagnostic system, which tells where problems are,” Jakobson said. “Larger and medium companies, their safety is a lot of times either safety manager driven or by the employee safety committee.”
With all customers, Jakobson said the company likes to stress safety and to help train users in operation.
In the future, Jakobson said leaders at Custom Industrial Products are consistently looking at different products and ways to make their products more efficient at the same time more sustainable to match with green initiatives by companies.
“We are constantly looking for different products to help us out and to move forward and change,” he said.
About the Author:
Eileen Schmidt is a freelance writer and journalist based in the Greater Milwaukee area. She has written for print and online publications for the past 13 years. Email [email protected] or visit eileenmozinskischmidt.wordpress.com to contact Eileen. If your company would like to be featured, email [email protected]