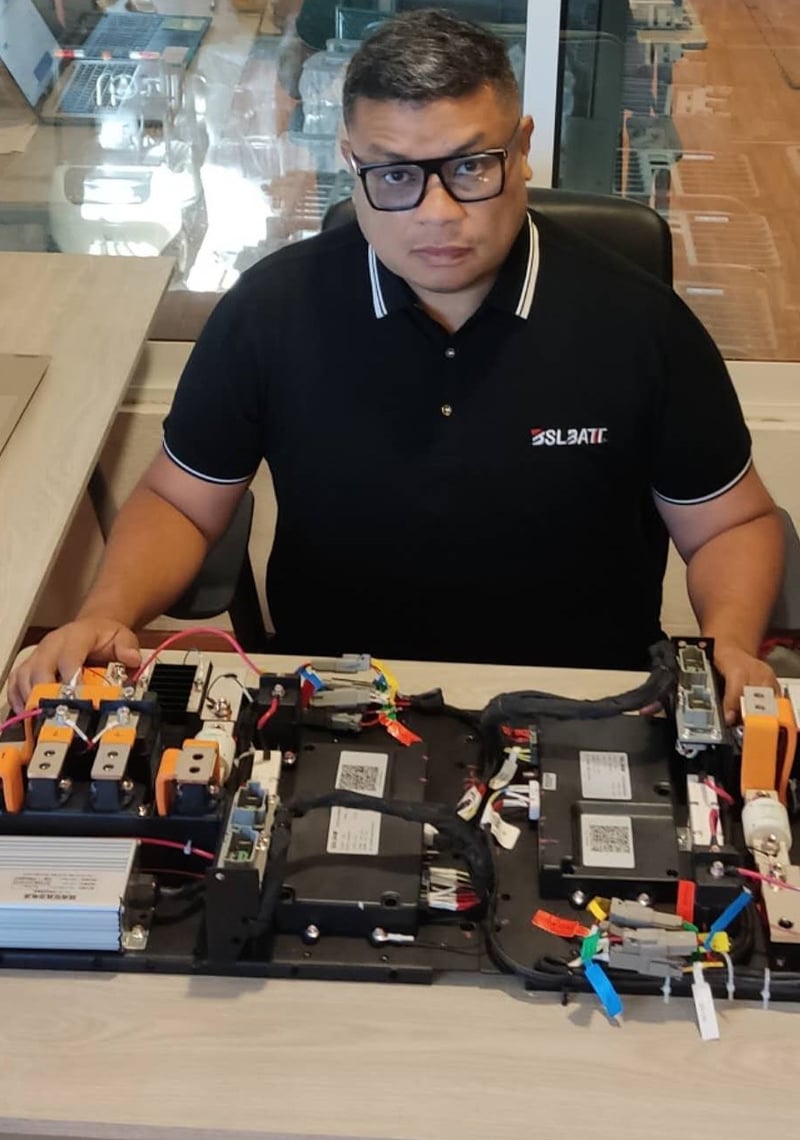
Know the differences and functionalities of battery management systems
1/6/7F-1 Building1 Zhongkai Innovative Base
Huifeng 6th Road ZhongKai Hi-tech Zone
HuiZhou City, Guangdong, INTL
http://www.lithiumforkliftbattery.com
Batteries used in forklifts and other material handling equipment often look very similar, with no obvious differences in design or features. A vehicle’s voltage, Ah capacity, and other technical indicators must meet the requirements of the main vehicle standard. However, there are often significant price differences between brands, not only due to the functionality of the battery management system (BMS) but also because of other parts of the “total product”: delivery and installation, integration with forklifts and chargers, and support, service and parts availability. For optimal performance and longevity, it is crucial to choose a lithium forklift battery that is reliable and safe. Your organization’s efficiency can be maximized by choosing the right battery for your device.
How do cheap industrial lithium batteries remain cheap?
When production expands, cheap overseas labor may be a major factor in retail prices. Material handling, however, is a relatively niche market. This advantage is offset by higher shipping costs and longer delivery times. After that, what happened?
First and foremost, it is the limited functionality of non-automotive-grade high-quality battery modules and base-level BMS. Secondly, the CAN bus system is unstable and the components are of high quality. Industrial lithium batteries are affected by these factors. The battery core is the heart of the battery, according to BSLBATT. We work hard to extend the life of our batteries and increase their energy and power density by using only the highest quality batteries with the safest technology. Even in extreme weather conditions, it operates over a wide temperature range. Furthermore, advanced BMS prevents battery degradation by providing real-time diagnostics, adjusting individual cell charging, and protecting and optimizing the battery.
Furthermore, the Advanced Controller Area Network (CAN bus) is the battery’s nervous system for communication. In addition to communicating battery condition information to the BMS system, the CAN bus functions as a central network hub. Additionally, high-quality components prevent overheating during high-current charging and discharging. In order to maximize the performance of the battery system, BSLBATT forklift lithium batteries are designed with the highest quality components. Process of charging and discharging. The lithium battery module, BMS, CAN bus system, and high-quality components cannot be adjusted according to the customer’s actual working conditions. Moreover, there are no advanced features, which may result in a price advantage, but may also cause battery users problems.
As you will see in the practical example below provided by David Zabala, a professional electrical engineer and top forklift expert at one of BSL’s distributors in Mexico, cheap industrial lithium batteries purchased online from overseas arrive at your doorstep just as easily as forklift batteries. The TV remote control requires AAA batteries. No, it isn’t. A second forklift or crane is required to remove the old battery, and a technician must be trained to connect and test it. Inspections include connectivity, safety, and operational aspects. BSLBATT’s high-quality lithium battery brand price usually includes installation and setup costs. Due to potential service needs, labor costs for initial installation will continue to rise.
In the best case, the downtime cost is equal to the rental cost while you wait for the spare parts to arrive. The cost of downtime to business operations is the worst-case scenario if a replacement is not made quickly.
An industrial lithium battery purchased online had a problem
This is the story told by David, a professional electrical engineer and top forklift expert at a BSL distributor in Mexico. BSL distributor in Mexico provided a quote for 15 5,000-pound electric forklift batteries to a customer in Monterey. It turned out that BSL’s distributor in Mexico quote was $1,200 higher than “the Internet’s” price, so it lost the bid.
David’s personal profile: https://www.lithiumforkliftbattery.com/bsl-batteries-north-america.html
A month later, the customer received a 20HQ industrial lithium battery and lithium battery charger from the public transportation company, but the old battery in his forklift couldn’t be replaced. If he orders through BSL’s distributor in Mexico, the new battery will be delivered and installed, and the old battery will be removed and properly disposed of. Instead, customers pay BSL’s distributor in Mexico $220 per battery for installation.
The customer experienced battery failure approximately 90 days later, contacted the manufacturer, and had a replacement battery accessory shipped to him. In this call, the customer asks David for help with replacing the damaged parts for a service fee of $500. While customers waited for their units, the only forklift stopped again. The rent ended up costing him nearly $600. He also experienced headaches and downtime, as well as the time it took to overcome these obstacles.
“So we spent an extra $1,500 upfront, so he bought the battery from the Internet,” David said. Once all is said and done, the customer shows that he understands local support for the product and won’t make the same mistake again.”
What is the best strategy for industrial lithium batteries?
According to David, most forklift dealers in Mexico do not use lithium technology at all. Many of them are making their own batteries or relying on artisanal battery producers who have not yet fully developed the technology they use. There are significant safety concerns with these batteries, and many battery systems today look as if they were cobbled together with jumper cables. Today, too many companies are playing with fire! To help more forklift dealers choose the best industrial lithium battery, I feel it is necessary to elaborate on four points. It’s not comprehensive, of course, but if a vendor can’t answer your questions in these areas, then they aren’t worth working with.
Safety is more important than price
● There is a wide range of battery technologies available in terms of cost and safety. I recommend paying the premium. Battery accidents are dangerous and, in my experience, more expensive in the long run than buying safe, high-quality batteries. For the peace of mind of our customers, all BSL products have passed the most stringent UL2580 test and every product is covered by PICC insurance!
UL2580 test certification
video: https://www.lithiumforkliftbattery.com/lithium-forklift-battery-ul2580.html
● Contact the supplier for accident statistics or speak with other customers who have used the battery for a long time. Temperature and cooling management should be checked
● Like people, lithium batteries prefer temperatures around 25°C. The most important parts of battery design are the temperature and battery management systems (TMS and BMS). Performance can be degraded by high and low temperatures and may even be permanently damaged.
● Venting is the last step before a fire occurs, which can cause permanent damage to the battery. It’s a big red flag if you’ve heard about battery outgassing from your supplier.
● Liquid cooling systems are adjustable, so you can heat and cool the liquid. Regardless of the ambient temperature, this allows for optimal performance.
● Avoid batteries without active temperature management.
BSL heating system for cold storage
BSL battery high and low temperture test
A compact fan for cooling
Examine the packaging closely
● You should look for printed circuits, not loose wires. It is more likely that a device will fail if there are more visible and present wires.
● Inquire about the fire safety and fire protection measures in cells. To ensure fires are contained, the best companies have fire response plans and safety systems in place.
● Companies that make great efforts to cool should be paid attention to. It’s probably the biggest difference in battery management – I can’t stress it enough.
● It should be very difficult to access the battery. The systems are high voltage and high current, and should not be exposed to the elements. Packaging should be designed with as much redundancy as possible.
● Parts made of plastic or molded indicate higher yields. Furthermore, the molded aluminum components indicate that the manufacturer has invested significantly in high-volume supply.
● Avoid battery systems customized for your application. You should choose modular products that can be used in multiple industries.
● Insulation plays an important role in managing battery performance. You should look for insulated containers and honeycomb packaging.
● Redundancy and safety are assured by the modular design.
Experience, field performance, and fine print should be checked
● Some equipment manufacturers make up to a dozen batteries at a time. In contrast, large battery technology companies have thousands of references and applications. Don’t mistake device application experience for battery knowledge. Complex systems are difficult to perfect.
● As a general rule, cycle life is expressed as a percentage of DoD “depth of discharge.” The standard is to provide cycle life as 80% DoD. The battery life will be skewed if it is less than 80%.
● The manufacturer should be able to tell you whether cycle life is theoretical or measured. Is it measured in a laboratory or verified on the ground? Only a few companies have proven field application data since the technology has only been commercially available for a short period of time.
As a conclusion
The technical specifications, dimensions, weight, connectors, controls, and appearance designs of industrial lithium batteries from different brands may be almost identical. Treating industrial lithium batteries as commodities, however, entails risks. There are primarily differences in mechanical and electrical design, electronics, and software, as well as local support and parts availability. For operators to avoid potential downtime and additional labor costs, they must understand the benefits and trade-offs across the entire product line.
About the Author:
David Zabala is a distributor in Mexico of BSLBATT products at the MGS Montacargas Group.