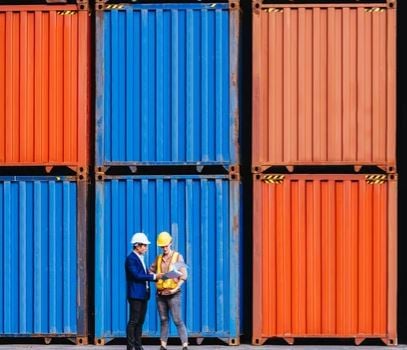
How is inflation impacting warehousing and the supply chain?
Until recently, high inflation has been more of a theoretical concept for many business owners and consumers. After all, it’s been decades since this country experienced severe inflation. But the past year has made inflation a major concern for consumers and supply chain partners. Here’s how inflation is driving up the costs of just about everything that impacts the supply chain and how your business can respond effectively.
How Inflation is Impacting Warehousing and the Supply Chain
Inflation measures the rate of an economy’s rising prices. When this condition exists, it impacts other areas, such as wages, demand, and the availability of certain services. Here is how inflation is affecting warehousing and the supply.
1. Shrinking Demand for Goods and Services
One common impact of inflation is a contracting demand for goods and services. In other words, as prices go up, people will buy less stuff. This will affect the need for things like warehouse space, labor, and transportation. If your business continues to produce or store the same amount of goods that it did in the past, it will probably end up with excess that it can’t sell.
2. Higher Materials, Transportation, and Labor Costs
Inflation doesn’t just impact the prices of goods on the shelves. It also drives up direct costs associated with things like raw materials, transportation, and labor. Some raw materials continue to be scarce, which affects pricing, and there are continuing labor shortages throughout the transportation and warehousing industries. Fuel prices are also a major factor in logistics, driving up freight and transportation costs that were already rising before driver shortages.
3. Rising Interest Rates and Less Access to Working Capital
Some businesses in the logistics industry rely on different sources of working capital funding to stay afloat during turbulent times. But when inflation is part of the equation, so are high interest rates. When the Federal Reserve continues to raise interest rates, this makes short-term borrowing unaffordable for small businesses.
How Warehouses and Supply Chain Partners Can Respond to Inflation
Many supply chain and logistics professionals are seeing how inflation is negatively affecting their business. These impacts include delayed orders, long lead times, price and rate increases, and supply chain instability. But businesses in these industries aren’t helpless. When facing these tough economic conditions, here are several ways warehouses and supply chain businesses can respond.
1. Become More Flexible
One of the best ways to persevere in times of economic uncertainty is to become as flexible as possible. How can you do this? First, if you are only dealing with one manufacturer, one shipping company, or one logistics firm, it may be time to diversify.
When you explore alternative suppliers, this can prompt your current ones to offer better terms. At the same time, you have a backup on hand if your preferred supplier is unable to meet their obligations due to various supply chain challenges.
2. Gain Insights for Predictability
The last thing you want to do during inflationary times is spend money on inventory you don’t need. It costs money to purchase items, transport them, and store them. And, if people aren’t buying stuff due to higher prices, this could devastate your business.
You can use insights from your warehouse management system (WMS) to better forecast demand for inventory purposes. Digital twins is another solution that allows you to simulate business performance in various scenarios so you can plot the most prudent course.
3. Improve Spend Visibility
How much visibility do you have into your current costs? If you have incomplete or inaccurate data, it’s time to address this matter before you run into a cash flow issue. Fortunately, some of the same insights that are providing better predictability can also help you improve spending.
When you review your insights, this provides an opportunity to discover various ways of eliminating or cutting costs. For example, you may be purchasing similar or identical items from different suppliers. You can consolidate shipping on items or explore other ways to streamline your operations.
4. Boost Supplier Engagement
Traditionally, supply chains have operated as a series of separate steps and business partners who communicated only as much as was necessary. In today’s environment, better collaboration between suppliers is the best way to streamline operations and save costs.
By opening the lines of communication with your suppliers, you can investigate alternative ways to accomplish your goals. For example, you may be able to get discounts for using a certain shipper or waiting a few days extra to have your items combined with another order.
5. Leverage Automation Solutions
Digital solutions enable warehouses and other supply chain partners to get the most out of every dollar they spend. For example, warehouses struggling with labor issues can employ various automation solutions to do more with less.
RFID, WMS, and other integrated software solutions can deliver cost savings to businesses that mitigate the impact of rising costs in other areas. The use of automated vehicles and equipment can reduce repetitive tasks, which also reduces the number of employees required to do a job.
Inflation directly impacts manufacturing costs, logistics, and many more areas associated with warehousing and the supply chain. When inflationary conditions exist, the supply chain may not run as smoothly as it should. But supply chain partners can implement solutions to improve flexibility, visibility, and predictability to achieve the best overall results in even the most challenging conditions.
About the Author:
In 2005, Newcastle Systems, Inc. was the first U.S. company to introduce mobile powered industrial carts to support supply chain applications, bringing leading-edge efficiencies to the market. The company has continuously pioneered new technology developing the first swappable lithium battery system for industrial applications in 2016, as well as the most ergonomic mobile carts available. A privately-owned, Massachusetts-based company, it serves some of the largest retailers, manufacturers, and distributors in the world to help to increase supply chain efficiency by consistently doubling employee productivity while reducing costly labeling errors by over 92%.