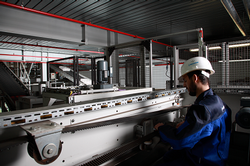
BEUMER Group: Using a modular system to provide customised intralogistics solutions:
In the field of intralogistics, the trend towards automation is continuing at full pace. In order to increase their competitiveness, companies want their plants and systems to work more efficiently and safely. At the same time, workplaces are required to be designed more ergonomically.
Additionally, the emergence of Industry 4.0 integrates all of the involved people, systems, machines and products into one dynamic network. This allows customers to better organise and manage their logistics value chain. BEUMER Group leverages a modular standardisation concept to offer customized solutions for individual tasks.
“Intralogistics is experiencing a transformation due to demographic changes and also because of increased process complexity. Automation technology in particular is constantly pushed forward,” recognizes Franz-Joseph Kleigrewe, Head of Automation at BEUMER Group. This way manual processes can be optimised and effective synergies formed between man and machine. “Automation technology is the key to technical development and progress,” Kleigrewe is convinced.
There are three equally important factors involved in the development process of automated systems: Customer orientation, innovation and standardization. If the focus is customer-oriented, the result are typically tailor-made solutions that can rarely be used for other projects. Focusing on innovation offers both opportunities and risks: innovation creates competitive advantages, but also poses the risk of increasing costs and postponing deadlines. One thing is clear: without innovative projects, there is no progress. Forward progress is why these projects need to be done regularly, while being aware of the potential risks. The procedure for standardised solutions is very different. They have been tried and tested. The customer receives an inexpensive and functionally reliable system, which can go live in a short period of time.
Standardised, yet tailor-made This can be a challenge. The customers’ requirements can be very specific. Each industry is different: from non-metallic mineral processing to chemical and mining industries, from CEP services to airports. National regulations and factory standards differ as well. At BEUMER Group, customized machines and systems are therefore created from the modular
system: the mechatronics modules for mechanics, electrics and software are adapted to the customer’s requirements.
“Operators no longer wish to run just one machine, they want a process: a combination of several coordinated systems,” Kleigrewe recognises as the market need. This includes filling, packaging and palletizing solutions: BEUMER Group offers the BEUMER fillpac, a filling machine particularly for
the building materials industry. Users can flexibly integrate and adapt it to existing packaging lines. Depending on project requirements, BEUMER Group offers varying designs. “We can provide this filling system with special weighing electronics, for example, coming from the modular system,” Kleigrewe explains. It ensures the weight accuracy of the bags. Depending on the application, BEUMER Group provides the system as a rotary or inline filling machine, with bag discharge line, bag placer, different number of filling spouts or devices for material feed and spillage transport. As a systems supplier, the company offers the BEUMER paletpac and BEUMER robotpac construction series, two different palletizing solutions that guarantee efficient stacking of filled bags. They can be provided with functionalities such as bag and empty pallet transport
systems, from the modular system. Depending on the product characteristics, the BEUMER paletpac is equipped with either bar-type, clamp-type or twin-belt turning devices. They turn the bags rapidly and gently to the required position. The high-capacity packaging system, BEUMER stretch hood, is BEUMER Group’s efficient solution to package the pallet stacks quickly and safely. The system provider offers them in different designs, with a varying set of sophisticated features.
Sortation and distribution – customized Whether mail or parcel service providers, airports or food industries – the requirements of sortation and distribution technologies vary widely. Especially for mail and parcel service providers, the material handling technology in distribution centres becomes increasingly complex. Sortation and distribution systems must be able to handle increasingly complex tasks and often adapt to different local conditions. Highly efficient processes are necessary to ensure quick delivery of packages to the customer. Some of the reasons are the changing consumer habits and trends, such as the growth of e-commerce. BEUMER Group offers different solutions including cross belts, Tilt Tray and E-Tray sorters. Depending on the application, these systems can be provided with modules and functionalities from the module unit, such as scanners, feeding posts, different induction units and discharge systems, balances or DWS systems.
Software from the modular unit
BEUMER Group has developed the modular BG software suite, offering users optimum and continuous control of their material flows. It can be customized to the user’s requirements. Products from other companies can easily be integrated. Its name, BG, stands for BEUMER Group and the software suite is a superior data processing system. Users can extend this modular solution at any time and optimise their material flows. Process data or reports are displayed on the BG Fusion user interface that works for all programs. Users can access all available data, without having to switch between the applications. They can also use the BG software suite on mobile devices, such as tablets.
The BEUMER Group Warehouse Control System (BG WCS) module allows you to connect the BG software suite to the warehouse management system or the ERP system of the customer via a network connection. This way, BEUMER Group ensures the communication between the different control levels for the user. As a single-source provider, BEUMER Group can create an intelligent connection between the individual systems, and integrate them into existing process and inventory control systems. The customer receives everything from one single source. The risk for error sources that could result from interfaces is avoided. Technicians carry out the electrical
installations, as well as the integration of the machine and system controls. “We also offer support during commissioning,” says Kleigrewe.
Customer-focused engineering
“The equipment and systems for our customers fulfil the required functions,” says Kleigrewe. “But we also observe our customer’s standards.” One of the customers is an international manufacturer of petrochemical products. As a single-source provider of filling, palletizing and packaging systems, BEUMER Group provided them with a complete packaging line. This includes a form fill seal system (FFS system), the BEUMER paletpac palletising system, and the BEUMER stretch hood high-capacity packaging system. It also includes conveying technology for the pallets, SCADA, a warehouse control and a warehouse management system, a guiding system for the fork-lift driver and a yard management system. “We are in constant dialogue with the user to work out the
requirements and match them with our modular system,” describes Kleigrewe. “The result is a customised solution.”
Industry 4.0 – high expectations
“The increase in networking and automation brings us on our way towards Industry 4.0,” says Kleigrewe. It creates highly interlinked system structures with a high number of involved people, IT systems, automation components and machines. The users can significantly improve the organisation and control of their logistics value chain. The system, machine and product controls must be horizontally and vertically integrated into dynamic communications networks. This creates digital engineering consistency through the entire logistics value chain – in other words: it is about the intelligent networking in the supply chain. “Making this possible in Industry 4.0 requires the development of powerful, linked sensors and actuators. This networking, however, leads to enormous amounts of data and metadata along the logistics value chain,” explains Kleigrewe. Another factor is globalisation: data management is now spread out over different locations, countries, even continents. Horizontal and vertical interfaces can quickly become cost drivers in factory automation. “Cloud computing offers an efficient technological base for holding data,” says the automation specialist. This service can replace or expand existing structures. Cloud computing also allows you to process significantly larger data volumes compared to traditional server solutions. In addition, real-time data can be synchronised with historical data. Uniform interfaces of the cloud services are currently in development.
The software interface standard OPC (Unified Architecture) is useful for making data available between all systems of a company. “It meets the most important requirement for data communication in Industry 4.0′” explains Kleigrewe. “This standard allows you to establish the communication between devices, controllers and applications, regardless of the individual driver. OPC UA can be directly embedded into devices, sensors and controllers. Data from different, non-compatible and open standards from different areas can also be transferred.
What will the future look like? Kleigrewe has a clear idea: “The processes in distribution centres will run fully automatically, from order to delivery, around the clock, seven days a week. This changes the requirements completely, and we are already experiencing this change.”