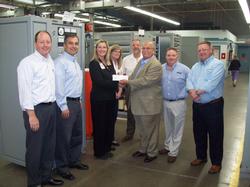
Ametek Prestolite Power awarded International Organization for Standardization (ISO) certification
AMETEK Prestolite Power, a leader in industrial battery charging and fleet management solutions, today announced it has successfully met the strict requirements conforming to ISO 9001:2008, a set of worldwide-accepted standards for quality established by the International Organization of Standardization (ISO) for the manufacturing industry.
The Troy, Ohio-based company received the “Certificate of Registration” to the ISO standards by Intertek, an independent certifying body, following an application process of several months to validate AMETEK Prestolite Power’s efforts to continually improve and keep focus on operational excellence.
Earning the ISO 9001:2008 certification is a “significant milestone in our company’s history,” said a proud Jim Lichtenberg, Business Manager for Prestolite Power. “It sets us apart from other charger manufacturers while certifying that our processes and procedures are up to world-recognized manufacturing standards.”
By being ISO certified, AMETEK Prestolite Power complies with various international standards, such as product quality, environmental friendliness, safety, reliability and economy. ISO 9001:2008 standards are designed to give consumers confidence when buying products from a manufacturer.
Lichtenberg noted that prior to certification Prestolite Power had always followed ISO standards’ guidelines for many of its critical procedures. “We have not changed our quality assurance processes, such as final testing and quality control testing, equipment calibration and process monitoring. Those were in place long before the ISO certification process began several months ago.”
He added that the ISO certification process requires regular internal and external audits to verify that the company is meeting the standards and performing as expected while identifying areas for improvement.
“ISO standards focus on customer perspectives and requirements, so by meeting these standards our processes will remain stable as we continually provide quality products to our customers,” concluded Lichtenberg.