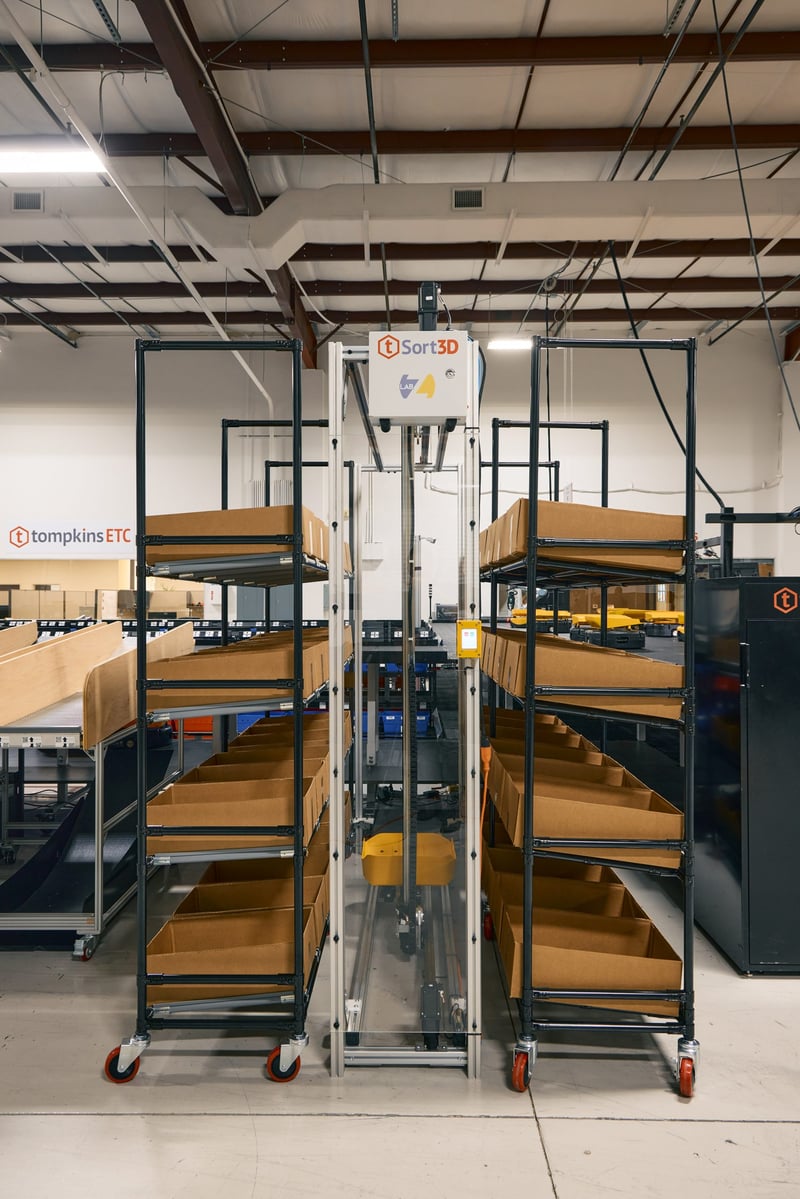
Tompkins Robotics continues to enhance Automated Sortation Process with new tSort3D System
In keeping with the belief to deliver adaptive, flexible, and portable solutions, Tompkins Robotics introduces the new tSort3D. tSort3D is modular, allows customers to implement quickly, and the system can grow and change as their operational needs evolve. The tSort3D greatly multiplies the destination density and volume of the sortation process. A tSort3D system is mated with the Tompkins Robotics tSort solution for item sortation loading and routing the items to tSort3D modules for order consolidation.
The system is ideal for the fulfillment of items for customer e-commerce orders and other fulfillment flows such as store replenishment and reverse logistics. The system can be deployed in a scalable fashion in sites as small as the backroom of retail stores and up to very large Distribution and Fulfillment Centers. tSort3D allows 6 to 8 times the sort destinations in the same space as other traditional automated sortation solutions, provides for thousands of sort destinations, volumes up to 20,000 an hour, and facilitates a single, very large batch pick. These capabilities far exceed other dense sortation systems on the market today. This solution solves a pressing need in distribution and fulfillment operations that no previous automation solution fully addressed.
“tSort3D can handle the widest range of products compared to other automated sortation solutions on the market,” says Tompkins Robotics President & CEO, Mike Futch. “The tSort3D uses a tray as the carrier, while other solutions use a cross belt. Tompkins Robotics unique tray design ensures that round, cylindrical, and oddly shaped items are compatible with our system.” In addition, tSort3D can handle wider, taller, and deeper products than other dense, robotic sorters on the market. The system can continuously track items, orders, and order status to provide real-time updates to an operator. tSort3D provides a much less labor-intensive process from picking through to order delivery to packing for many product flows and products. Completed orders can be removed individually or as a batch of up to 24 orders. The system greatly enhances the productivity and capacity of an operation while taking up less space, deploying in less than half the normal required time, and costing less. In addition, the system is very flexible having modular, scalable configurable, and portable abilities that are unique and not found in other solutions.