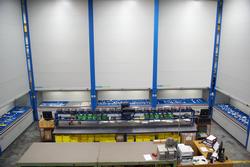
May the (labor) force be with you
As the human workforce ages and shrinks, automated storage and retrieval systems can help to maximize warehouse associates’ productivity levels while reducing overall labor requirements. Between the end of World War II in 1946 and 1964, in the U.S., 76 million babies were born – the largest in American history – the baby boomer generation.
Their numbers had a dramatic impact on the domestic economy, raising home ownership, consumer spending and employment rates to unprecedented heights. As baby boomers retire, however, so does the available workforce. The U.S. labor force participation rate (the percent of the adult population that is either employed or seeking a job) has been steadily declining since the late 1990s. With a declining overall U.S. population, there simply aren’t as many individuals as needed to fill job openings in manufacturing, material handling and logistics.
To compensate for these workforce challenges – fewer workers and the skills gap – more companies are investing in automated solutions. These technologies help to both reduce the physical demands of warehouse activities, as well as streamline and organize the required tasks for better productivity with fewer workers.
Automated storage and retrieval systems provide highly dense storage in an extremely compact footprint. Three primary types include horizontal carousels, vertical carousels and vertical lift modules (VLMs).
Automated storage and retrieval systems maximize associates’ time and productivity when filling orders in a variety of ways. Among them:
Elimination of travel time. Travel to pick faces in a conventional, manual fulfillment operation is time consuming. Alternately, automated storage and retrieval systems present stored items directly to an operator via the “goods to person” methodology. This eliminates time spent walking from one pick location to another within a warehouse. A pod (or group) of machines can be picked from by a single operator, dramatically increasing picking speed and accuracy with significantly lower labor requirements.
Improved Ergonomics. Manual picking operations require a great deal of physical effort on the part of associates: bending, stretching or reaching to retrieve an item, for example. Picking items from drawers or shelves might also require lifting, bending, walking, pushing, pulling, twisting, stooping and climbing on ladders or stepstools. Conversely, every item stored in an automated storage and retrieval system is delivered to the operator at the correct ergonomic work height, called the “Golden Zone” (waist-high). This substantially reduces the chance of worker injury and its associated absenteeism, insurance premiums and claims for worker’s compensation.
Reduction of search time. Once an associate arrives at a pick face, time must be spent searching the racks or shelves visually to locate the correct item, then verify the stock keeping unit (SKU) and required quantity. Conversely, automated storage and retrieval solutions are equipped with light-directed systems that highlight the item’s location and quantity required for picking (or replenishment), eliminating search time and boosting accuracy.
Error prevention. In addition to indicator lights, automated storage and retrieval systems feature integrated message centers that communicate pick information to the operator. Together, these systems indicate the precise location within the carrier of the item to be picked, display the part number or description and specify the required quantity. They can also show a photo image of the required item, giving an operator clear visual cues that can help to verify the correct item has been picked.
Optimized picks. In manual order fulfillment operations, pickers often just fill one order at a time, achieving pick rates of approximately 50 lines per hour. For faster throughput, automated storage and retrieval systems utilize both inventory and order management software, sequencing picks so all items are picked in one rotation, or cycle, other machine’s storage bins or trays.
They can also leverage batch picking, grouping orders with a common item or items together for simultaneous selection. Multiples of the same items are picked then delivered to a nearby workstation for sorting into appropriate orders. Because multiple orders can be filled at the same time, batch picking can increase throughput by as much as 200% – up to 600 lines per hour.
Fast Training. Facilities that utilize seasonal hiring to accommodate spikes in customer demand experience considerably shorter training time with automated storage and retrieval systems, largely due to the indicator lights and integrated message centers. A temporary worker unfamiliar with a facility’s layout can be stationed at an automated storage and retrieval system for highly productive picking after just a brief introduction to the equipment.
All of these functions can optimize an existing labor force, increasing productivity from 200% to 600%. Because an automated solution enables just one worker to handle the picking assignments of multiple operators, as many as two-thirds of a facility’s workforce can be reassigned to other, non-picking tasks, without a loss of throughput. Alternately, implementing these automated storage solutions can compensate for a scarce and declining labor pool – a trend that will only progress as baby boomers continue to retire, and take their valuable skills with them. By implementing one or more automated storage and retrieval systems, an operation can maximize the productivity and efficiency of its existing labor force – particularly skilled associates – by minimizing the amount of time it takes to pick orders.
Kardex Remstar, LLC, a company of the Kardex Group is a provider of automated storage and retrieval systems for manufacturing, distribution, warehousing, offices and institutions. For information about our dynamic storage solutions, call 800-639-5805 or visit www.kardexremstar.com.