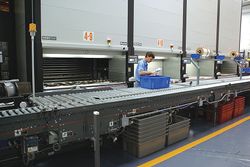
Connecting ASRS islands of automation
Deployment of automated storage and retrieval systems (AS/RS) has been delivering impressive improvements in labor or space savings within facilities for decades. Reducing the number of workers needed for picking, or freeing up space by moving to high density storage are key areas of payoff and justification for these AS/RS systems. Today, the larger struggles for distribution center (DC) operations tend to be around customer service expectations.
Companies find themselves with several islands of automation, each providing ROI to the intended area, but these disconnected islands make it difficult to meet bigger order fulfillment challenges. Integrating AS/RS with other technology investments can improve processing and picking, support batch or zone picking and coordinate picking with host WMS or ERP systems so picking from AS/RS can be consolidated with manually picked items from other zones.
To support just-in-time (JIT) order fulfillment, Mazak Corporation’s DC uses 15 Shuttle XP Vertical Lift Modules (VLMs) from Kardex Remstar grouped into four pick and pass workstations. A motorized conveyor line connects each VLM workstation and zone. Orders are picked into totes which travel down the conveyor to the next zone that has items needed for that order before ending up in the pack/ship area.
The DC’s order fulfillment process starts with customer orders coming into Mazak’s order management/WMS via multiple means. Once an order is placed, the WMS passes the order to the Kardex Remstar Power Pick Global software that manges the VLMs, to the systems in the packing area and to the system of the overnight shipping carrier delivering the order. “Basically, we’ve created an efficient, high velocity system that enables us, within 15 minutes of a customer placing an order, to email that customer a tracking number,” says Steve Trammel, North American Parts Center manager for Mazak, “There are different systems interacting, but we view it as a total solution for the customer.”
Use of the automated VLM’s has yielded benefits in labor versus its past methods which relied in part on smaller, manually operated VLMs, and the manual carrying of goods to the packing area. The move to the Shuttle VLMs, zone picking and the conveyor system allows Mazak to fulfill orders with five workers versus nine with the old methods, while helping it further increase the percentage of orders it is able to ship out to customers for next day delivery.
Ultimately, connecting AS/RS solutions to a host WMS or ERP system is being looked to as a means of accelerated order fulfillment. The goal is getting more product out the door quickly and accurately to satisfy customers who increasingly have come to expect next-day delivery. The point efficiencies of AS/RS offer real payback, but at the same time, AS/RS software integration helps companies meet more strategic goals around customer fulfillment, without having to ramp up the labor force.