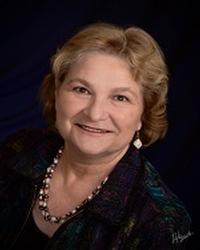
2018 trends call for tech-savvy, mobile industry
That question necessitates a multi-layered response. Efficiency, customer satisfaction and technology are at the core of the trends for the next year. As e-commerce, labor shortages and demand increase, so do the innovations within the materials handling industry.
Technology is the key component of the industry’s future. Mobile technology allows workers to move throughout the warehouse or facility. Not being tied to a stationary computer provides both flexibility and efficiency. Dirk Vonholt of TVH, a global supplier of quality replacement parts, safety equipment and accessories for material handling and industrial equipment industries, refers to the wrist scanners worn by employees as an example of a worker’s mobility being an effective use of time and space in the warehouse.
The workforce is becoming more tech savvy, consequently, coining a new phrase: gamification. Gamification is not a game. By using game mechanics to inspire employees, it is a way for them to monitor their progress at the workplace, thus improving both employee performance and the work culture. Gamification techniques use on-the-spot feedback rather than the typical monthly or even yearly evaluations. Transparency is an advantage of gamification strategies since objectives and key results (OKRs) are tracked and people can see the OKRs of others. Employees are able to monitor their progress at the workplace, use intrinsic motivation and change not only their performance but improve the work culture.
Autonomous vehicles are now common place within material handling. This will only increase. According to Mick McCormick, VP of Warehouse Solutions at Yale Materials Handling Corporation advances in navigation technology and software can enable standard lift trucks to function without an operator, producing a robotic lift truck solution that sheds the limitations of traditional vehicles. Laser based navigation technology produces a two dimensional view of the facility, measuring the building structure by looking for hard features like columns, walls and racking.
Mr. McCormick also believes that automation limits costly downtime. He cites a study by Information Technology Intelligence Consulting that found a single hour of downtime costs more than $100,000.00. These interruptions mean missed shipments, lost production time and lost costumers.
The CAN-bus (Controller Area Network) technology of Delta-Q Technologies (Amanda Yeo, Nikhil Iyer, Mourad Chergui) allows the autonomous vehicles to communicate with electrical components that control braking, fuel injection and other systems. This has been expanded beyond the blue tooth technology, enabling fleet management systems to extract charger data using CANbus, and become a part of the telemetry systems of the machine through cellular or Wi–Fi connection. With these technologies, warehouse management systems will perform once time-consuming scheduling and maintenance consistently to save operating costs.
According to Erich Carter and Mark Wilkinson of Indigo Software, warehouses run entirely by robots are not probable for many small and mid-sized operations. However, the McKinsey (a global management consulting firm) study has projected that 57% of existing warehousing and logistic functions will be automated. Without automation many managers must spend a large portion of the day on firefighting activities or worker management. Automation and artificial intelligence will change that scenario, as managers will be able to step away from operational work and focus on their original assignment of strategic planning to ensure high customer satisfaction.
The fear that the advances in technology will mean mass unemployment is unrealistic. Adaption to an environment in which employees work with machines will require analytical skills that will give rise to new jobs that are not in existence today. History proves that while short-term unemployment may result, in the long-term new jobs require more employees. Without this progress, stagnation and the permanent loss of jobs are the inevitable outcomes.
Businesses today are inundated with data each day. Being able to effectively collect and then competently use this information is the challenge of “Big Data.” Mr. Vonholt considers the use of Big Data to be a useful and efficient function of marketing and advertising. As an example; targeting email campaigns rather than using the blanket system of emailing potential customers is more cost effective. In addition to the world of Big Data is The Internet of Things (IoT) that includes sensors and data collection technology built into physical objects for machine to machine communication.
Mr. McCormick maintains that the amount of data is unprecedented with the possibility of as of yet unrealized productivity. This productivity requires that the information be vetted and applied constructively across an entire operation. Yale Vision telemetry offers a wireless asset management system to track and report on the status of every truck in the fleet, thus maintaining a visibility that once required time consuming manual processes.
The IoT connects not only machine-to-machine but people-to-people and people-to-machine. According to the analyst firm Gartner, there will be 26 billion connected devices by 2020. That means four devices for every human on earth. Cam Davies of OTTO Motors, a designer, manufacturer and operator of self driving vehicles for industry, thinks IoT will be the standard and will need to be in an open format that can be read and leveraged in two way communication with automation platforms. Big Data and IoT will allow for predictive maintenance applications including data from the entire factory. Other applications may include the optimization of production schedules, the inclusion of supply chain data and limiting on hand inventory for a more efficient operation.
New energy sources will continue to make appearances in the next year. Warehouses constructed with skylights, light sensors and solar panels will become more common. A warehouse roof is an idle asset with ample space for solar panels. Solar energy can supply energy security, is cost effective, reliable and requires minimal maintenance. Murphy Warehouse of Minneapolis /St. Paul has installed solar panels on five of its sites. The panels take up only 2% of the surface area and provide 50% of the facility’s electrical needs. They then pass these savings on to their customers.
Lithium batteries are another innovation that has contributed to the evolution in the material handling industry. The lithium batteries will reduce costs, maximize up time and extend battery life. According to Delta-Q, more than 2 million vehicles and industrial machines presently using its chargers for both lead-acid and lithium batteries. These charging systems are also capable of operating under difficult situations and increase on time delivery ability.
Since lithium batteries can be repeatedly charged to 100% capacity, operators can spend more time on the job. Mick McCormick points out that lithium batteries can be charged anywhere at any time with a standard 120 volt outlet including during in transit travel on a trailer to a delivery site. They also are engineered to last five years, so fewer batteries are needed over the life time of a lift truck. They contain no acid and require no water or cleaning, subsequently are maintenance free.
Hydrogen is the most common element on earth. Hydrogen fuel cells generate clean power and are useful for a broad range of applications, so this innovation might also be the wave of the future. For sustainability the hydrogen fuel cell meets many criteria. It eliminates the need for battery chargers and produces no emissions. Mr. McCormick states that they only require three minutes to refuel so operators can return to work quickly.
The role of e-commerce in material handling is enormous as more customers demand same day delivery. Brian Neuwirth, vp of sales and marketing for UNEX Manufacturing says that warehouses will have to redefine their processes to keep up with order picking operations and optimized storage. Another factor he believes is important to note is the labor shortage. It will be mandatory for warehouse managers to lower labor usage. UNEX offers solution to speed order picking operations such as their patented Span Track that reduces travel time by 85% between picks to speed fulfillment of orders. Dirk Vonholt suggests that building more warehouses closer to distribution centers can help solve the problem of slow delivery. The expenses and delays associated with air transport means that more warehouses is a more efficient solution.
Sustainability has become a more important aspect of material handling and will continue to become a dominant theme within the industry. As previously stated solar and wind power along with hydrogen fuel cells contribute to sustainability but worker sustainability must also be considered.
Cam Davies states that facilities with more automation have more employee retention. That in turn creates a better culture and an environment in which employees know one another and care about their lives. In this environment managers have an easier time hosting culture focused events such as team volunteering, professional development sessions and team outings. As general labor jobs transition into knowledge worker jobs, facilities will evolve to more satisfying and rewarding work and workplaces.
TVH has instituted green initiatives such as recycling within the company but has also emphasized healthy living for its employees. Stop smoking classes, a health clinic on site, free fruit days and a gym all contribute to a healthier workforce and therefore more employee retention. The company earned the American Heart Association Platinum Level Award for establishing a fit friendly workplace.
Mick McCormick cited a stark statistic from the Bureau of Labor Statistic. The turnover rate for warehouse workers is 36%. The cost of filling vacant positions is anywhere between 25% and 150% of an employee’s annual salary. These numbers make it imperative that operations re-evaluate how to deploy labor and implement technology. Using automated solutions for basic materials transport tasks frees the employees to advance to more engaging, meaningful positions. This helps address employee turnover and labor sourcing challenges. Improving the work culture has become an important trend for 2018.
Lights out Warehouses is an idea for the future. This means there are no human laborers in the warehouse. It is fully automated with only maintenance being serviced by people. Is this a probable scenario for the materials handling world? That depends on whom you question. Larger warehouses most certainly will be fully automated. Equipment such as UNEX’s Span-Track carton flow rollers, wheel beds and shelf tracks make the transition possible. An example of a fully automated warehouse, Zappos, was purchased by Amazon but not before they transacted $9 billion in business in 2009. Zappos could offer 365-day return policy, 24-hour delivery and free shipping with its totally automated system.
Not all companies believe total automation to be the perfect solution. Smaller warehouses will continue to depend on people within their facilities. More of the tedious, repetitive work will be completed by automated processes, however. This truth will change the composition of all warehouse workforces and bring a new reality to materials handling management.
The future of materials handling/supply management is replete with possibilities and opportunities. It is certain that with innovation and diligence, the industry will not only meet the challenges ahead but thrive.
Susan Miller Hellert is Senior Lecturer Emeritus from the University of Wisconsin Platteville. Now a free-lance writer for a variety of clients. You may email [email protected] with questions.