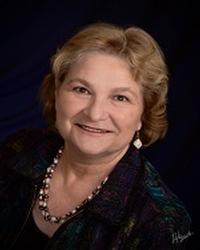
Warehouse technology drives cost down
Warehouse efficiency has always been an integral part of business systems. As costs and competition increase and profit margins decrease, this efficiency has become essential for the continuation of a company’s existence.
Methods of efficiency will eliminate unnecessary procedures as well as implement error reducing technology. Without warehouse efficiency measures the workforce must be increased exponentially to meet the constantly escalating demand for service.
A “Lights Out Warehousing” system is a totally automated process with few human workers. The lean plant operations approach is phased in automation over a period of time. Jeff Christiansen, vp of product at Seegrid, believes introducing a product such as self-driving vehicles is a low impact step in the automation process.
Causes of increased efficiency demands
E-commerce in 2016 reached $1.915 trillion with no ceiling in sight. According to the U.S. Census Bureau of the Department of Commerce for the second quarter of 2017 e-commerce sales reached $111.5 billion in the U. S. This was a 4.8% over the first quarter of 2017. Shea Bennett of ADWEEK on July 11, 2014 stated that $1.2 million was spent every 30 seconds on e-commerce business. These statistics verify the tremendous impact of e-commerce on business and therefore, warehouse efficiency.
Kevin Ledversis of Newcastle Systems maintains that the effect of e-commerce on warehousing has been huge. He cited the needs of next day delivery, customer satisfaction and the projection that e-commerce transactions will reach $4 trillion by 2020 as being the driving force in increasing efficiency within the warehouse.
Improved customer service demands an increase in efficiency within business. To achieve reliable shipping and timely deliveries to meet the rise in customer service demands that warehouses must adapt. In The role of electronic commerce in the global business environments (2014) K. Kasemsap stated that since perception is reality, excellent customer service is essential. One bad review can mean the loss of customers and impact the bottom line of a company quickly. Competiveness demands fast, accurate and reliable responses to orders, returns and customer comments.
Types of automated systems in the warehouse
Self-guided forklifts or self-guided vehicle (SGV) are autonomous, self-directed robotic delivery systems for the movement of products in diverse environments. They reduce labor costs because they require one-time investments but avoid costs of salaries, healthcare, taxes, vacation time, etc. Safety is another benefit as these vehicles have multiple built in safety measures. Humans in contrast can become tired, distracted or ignore safety directives. Since they can operate 24/7 they also increase productivity. Christensen advocates launching a pilot program with several self-driving vehicles as a first step in creation of a connected smart warehouse.
Automated storage and retrieval systems consist of a variety of computer controlled systems for automatically placing and retrieving loads from storage locations, such as high density multiple deep storage systems. These technologies maximize floor space, reduce labor and inventory requirements, increase ergonomics and increase accuracy.
Robotic palletizers and high speed conveyors improve efficiency in loading of products by funneling boxes toward the palletizing robots through a multiple conveyor system. They are then split into rows in preparation for palletizing. When the pallet reaches capacity it is removed by conveyor and an empty pallet is fed to the robot. These systems have proven to be both reliable and flexible.
Mobile robots are automatic machines capable of moving around within their environment. Included in this technology are mobile computers that allow operators more flexibility rather than requiring them to constantly walk back and forth from computers to work areas. Advantages of mobile robots include shorter cycle time due to the ability to work at a constant speed with no need for breaks, improved safety and better floor space utilization.
SelectHub details the benefits of Warehouse Management Systems and System Application Programming (WMS and SAP). They offer maximized labor resources, better demand planning and improved relations with customers and suppliers. Suppliers enjoy fewer long waiting times at the loading docks and customers gain reduced delivery lead time and fewer order inaccuracies. These systems also enhance security because they require employees to use individual accounts thus creating an audit trail that improves accountability and reduces the risks of theft.
Radio frequency identification technology or RFID uses electromagnetic fields to automatically identify and track tags attached to objects. Reasons for adopting this technology include inventory accuracy and improvement in picking and shipping times. Drones can be used to find items in giant warehouses. RFID tags replace bar codes. These tags don’t need line of vision to read and can include much more information than the bar codes. The drones can access high shelving without the inherent dangers of humans on ladders. They are ideally situated for large-scale repetitive tasks such as taking inventory.
Benefits of technology
According to Jeff Christensen of Seegrid: “In manufacturing and e-commerce environments, every human touch is costly and unpredictable. As we help our customers develop smart factories of the future, safety, efficiency and operating costs will continue to be the driving forces behind the adoption of automation.” “The Seegrid GP8 Series 6 self driving pallet truck allows distributors to change routes in-house, operate in manual mode and effortlessly scale their fleet as they grow. As a result pallet truck pick up and drop offs can occur without human interaction increasing productivity while labor shortages grow.”
Yale Materials Handling Corporation has introduced the MPEO8OVG end rider Driven by Balyo. It won the Gold Product of the Year Award at the Engineering Award in Manufacturing on April 3, 2017. This product uses infrastructure-free navigation technology to independently pick up, transport and drop off pallets anywhere on the floor – recognizing existing structural features to navigate rather than requiring operations to install tape, wire or other infrastructure. This enables easy adaptation to changing layout configurations and efficient route calculations. Able to switch to manual mode with the touch of a button, this lift truck enables operations to accommodate unexpected demands.
Cimcorp, a manufacturer and integrator of turnkey robotic gantry-based order fulfillment and tie handling solutions has supplied a robotic dolly picking system for Sinebrychoff of Finland- the 197 year old leading manufacturer of beers, ciders, soft drinks and energy drinks. A subsidiary of Carlsberg, international brewing and beverage company, Sinebrychoff plans to automate its Kerava, Finland location. The Cimcorp’s system replaces the order picking of dolly loads that until now has been a manual process and accounts for 30% of the company’s distribution deliveries. Automating this process represent a significant cost saving, as well as providing the opportunity to eliminate picking errors and thereby enhance customer satisfaction.
Sinebrychoff’s orders vary considerably. Whether the order consists of truckloads or single cases, the Cimcorp system can handle it plus any seasonal special products introduced. This fully automatic system entails no human labor until the product is loaded into delivery vehicles. Beverages are transported from high bay warehouses by conveyor to the dispatch area where a vision system will enable the products to be unloaded by universal robots and deposited on dollies or mini dollies. Automatically shrink wrapped, the loads are then stored by gantry robots and then picked by overhead robots according to customer demand. Laser guided systems transport the products to the loading area.
Customer satisfaction is a major component of Sinebrychoff’s decision as Kai Tuomisaari, sales director of Cimcorp stated: “The Cimcorp solution will ensure 100% picking accuracy and 100% product traceability, as well as providing flexibility for future changes”.
Kimmo Sormunen, automation manager of Sinebrychoff also stated that the energy efficiency of the robots is another important benefit. Efficiency is the primary goal of automation and reducing energy consumption means more efficiency according to Jeff Christensen. He continues that human operated vehicles often consume energy sporadically. Sporadic energy consumption ceases to be an issue due to the consistency of self-driving vehicles.
Safety is another aspect of technology in warehousing since every seven seconds an employee is injured on the job. Adding technology along with additional training and safety equipment will reduce this number for the benefit of the individual workers and the company’s profit margin. Steve Dew of Adrian’s Safety Solutions said, “Many of our material handling customers are working in highly active environments and simply do not have time for days of downtime while safely equipment is installed. Our products provide a simpler way to protect workers and products while keeping an eye of the facility’s bottom line.”
The use of laser scanners or cameras to read bar codes on a conveyor belt eliminates the need to perform repetitious actions. The automated system replaces the individual worker‘s requirement to move or lift products. The result is to obviously prevent potential worker injuries and, therefore, lessen compensation claims, time off work, and increase employee satisfaction.
Problems presented by automation
Kevin Ledversis of Newcastle Systems believes that fear of system hacking can be an obstacle to fully automating warehouse operations. As society becomes more interconnected due to advanced computer systems, the threat of hacking has increased. The recent hacking of Equifax, a credit reporting agency, has affected as many as 143 million Americans. The same danger is possible in warehouse management.
In Warehouse Automation: Risk and Reward (September 29, 2014) by Luke Atkinson Foley and Steve Phillabaum, intellectual property, data and identity theft are the major targets of hacking in a warehouse system. This can result in claims by employees against companies as well as the loss of confidence in a business by both clients and customers. The use of tablets throughout warehouses increases efficiency but exposes more information to infiltration. In 2014 3,000 U.S. companies experienced systems hacking resulting in a cost of $100 billion.
According to Christensen, another major obstacle is skepticism toward automation from employees. This can be alleviated by increased training, beginning on a small scale and the assurance that automation will result in consistent and reliable results.
Cost is another problem according to Foley and Phillabaum. Since the range of automation costs can vary from several thousands of dollars to millions, it is essential to complete a full evaluation of the scope and size of the warehouse and automated systems available. Other potential issues accompanying automation are distractions, data addiction and less operational awareness. To successfully combat these concerns, a business should not only ensure that all employees learn to safely operate the equipment, but also engage a risk management consultant.
Large maintenance budgets required by automated systems can be another dilemma, since a 24/7 presence is necessary according to Kevin Ledversis.
Myth vs. reality of technology in warehousing
Common myths attached to automation in warehousing are contradicted by Visastore Systems in their EBOOK 15 Common Myths About Warehouse Automation. While “Lights Out Warehousing” refers to a system in which no human labor is required, according to Visatore, it is important to note that not all systems are total. There are a variety of levels and costs available. These systems offer different pay off statistics. Basic programs for picking operations result in a short pay off period of 6-12 months, while fully automated systems may require 5-10 years or more to pay off.
Small warehouses often believe they are not large enough to profitably convert to automation. Warehouse Management Systems can benefit any size operation with significant benefits to accuracy, labor efficiency and productivity.
The loss of jobs is a common protest against automation. In reality, automation supports workers while removing monotonous, non productive and mistake prone tasks. As the number of qualified workers decreases due to age or a simple lack of interest in warehousing as a career, it becomes more difficult to secure skilled employees. Automation allows employees to acquire new talents and jobs within the industry mitigating the high turnover that is common in the warehouse field.
Conclusion
Automation within warehouse operations is a continually evolving process. Each business must evaluate the needs, costs, structures and projected results based on the best information available. The variety of systems, methods of installation, as well as the impact on employees and the profit margin are all important variables. It is a fact that automation is here to stay and growing. Whether adopting lean practices that incorporate technology in an already existing system or an entirely automated “lights out” system, the future includes automation.
History teaches us. Queen Elizabeth I believed it to be in the best interest of her subjects to deny a patent for an automated knitting machine. The machine, she thought, would deny hand knitters and weavers their livelihood. The machine came despite the royal action and by the end of the 19th century there were twice as many factory weavers as there had been hand weavers.
According to Sarah Kessler in the Optimist’s Guide to the Robot Apocalypse in Quartz, March 9, 2017, Amazon has increased its number of robots in their warehouses from 1400 to 45,000 while the rate at which they hire employees has not decreased. Technology creates new jobs. Jobs we cannot even anticipate today will exist tomorrow. She goes on to explain that in the United States at the beginning of the 20th century, 50% of all workers were in agriculture. Today that number is about 2%. There has been no massive unemployment.
In 1965 Gordon Moore stated that fast evolution of technology will continue to accelerate. The conclusion must be that those companies who don’t evolve are at risk of falling behind or worse failing completely.
Susan Miller Hellert is Senior Lecturer Emeritus from the University of Wisconsin Platteville. Now a free-lance writer for a variety of clients. You may email [email protected] with questions.